品質改善の進め方、重点指向や維持管理の考え方(PDCAサイクルとSDCAサイクル)を解説
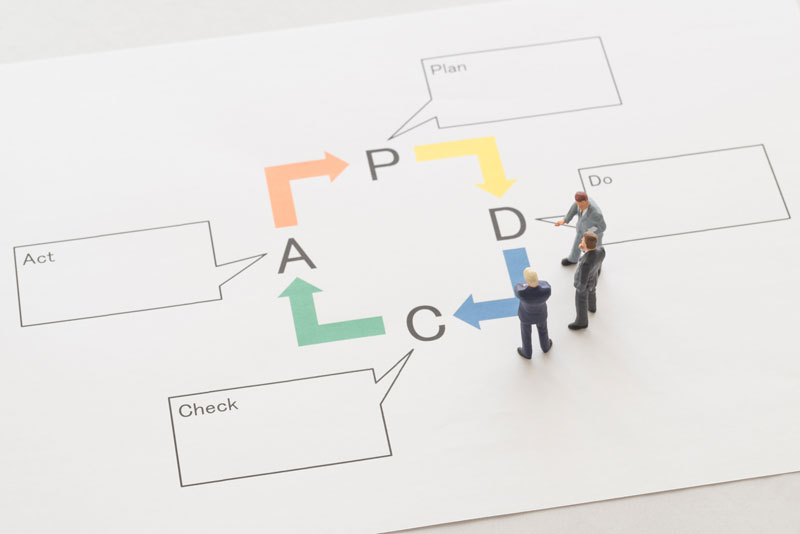

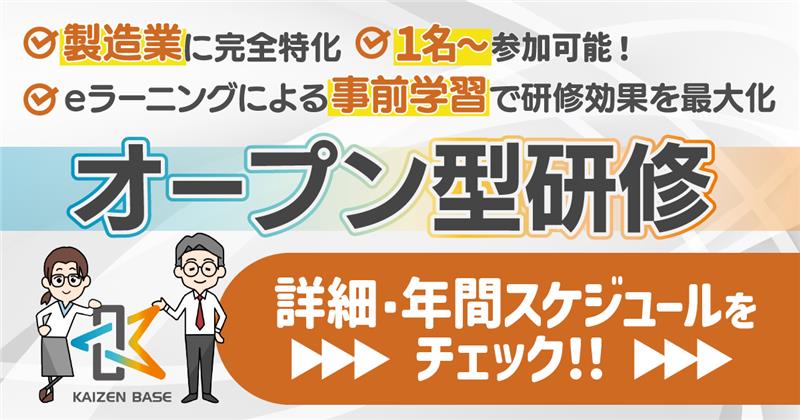
目次
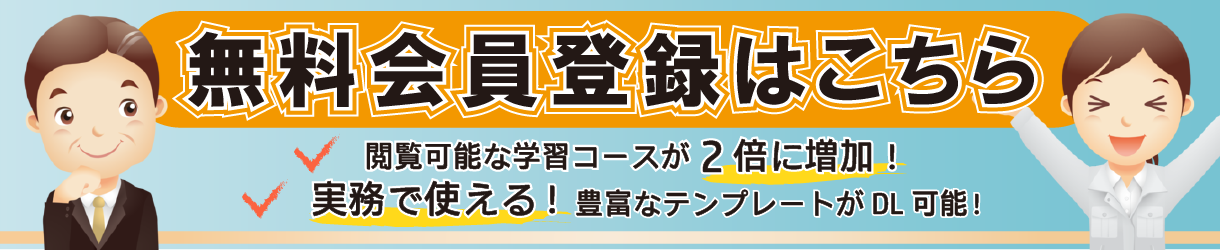
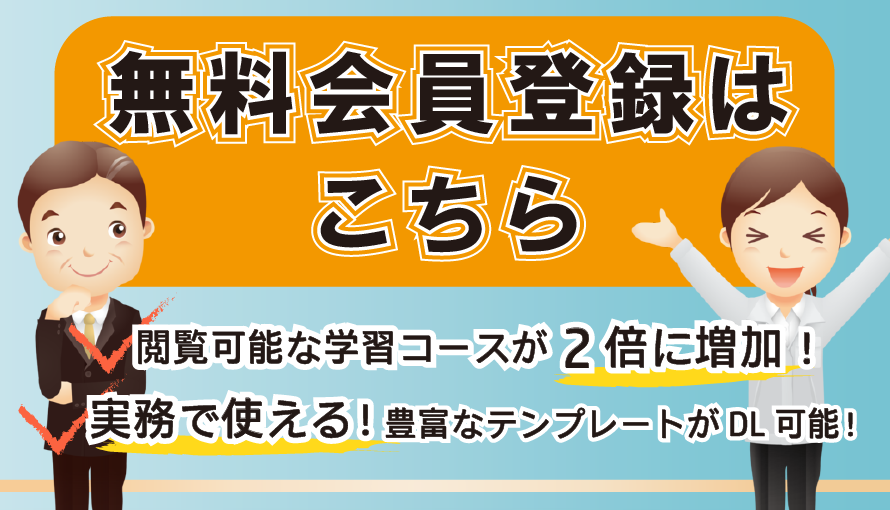
品質改善と維持管理の考え方とは
品質改善を行う際には、ただやみくもに進めるのではなく、重点指向で進めていかなければなりません。また、改善だけではなく、維持管理もセットで行わなければ後戻りしてしまいます。
本ページでは、品質改善を行う際のPDCAサイクルの考え方や維持管理のSDCAサイクルの考え方、重点指向のポイントについて解説しています。
維持管理と改善
改善だけでは後戻りしてしまう
まずは、維持管理と改善について確認します。
品質管理においては、維持管理と改善の2つの視点を継続していかなければなりません。
一般に、維持管理だけを行なっていても、水準の維持にしかなりません。
一方、改善だけを行なっていたとしても、水準向上どころか水準が低下してしまうことにもなりかねません。なぜならば、管理により定着させなければ、「後戻り」してしまうからです。
せっかく改善により良くなったとしても、後戻りしてしまったのであれば、行なったその改善すらも無意味なものになってしまいます。
従って、改善を行なったら、それが維持定着するように管理を行なう、という両輪で進めていくことが基本です。
改善と管理を継続的に行ない、常に水準が向上し続ける職場を目指していくことが大切です。
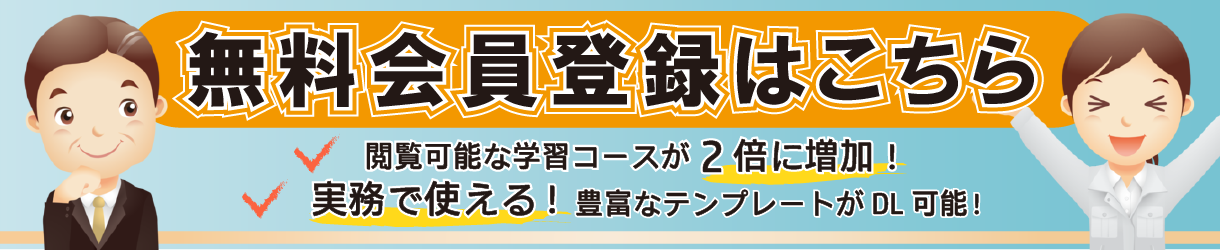
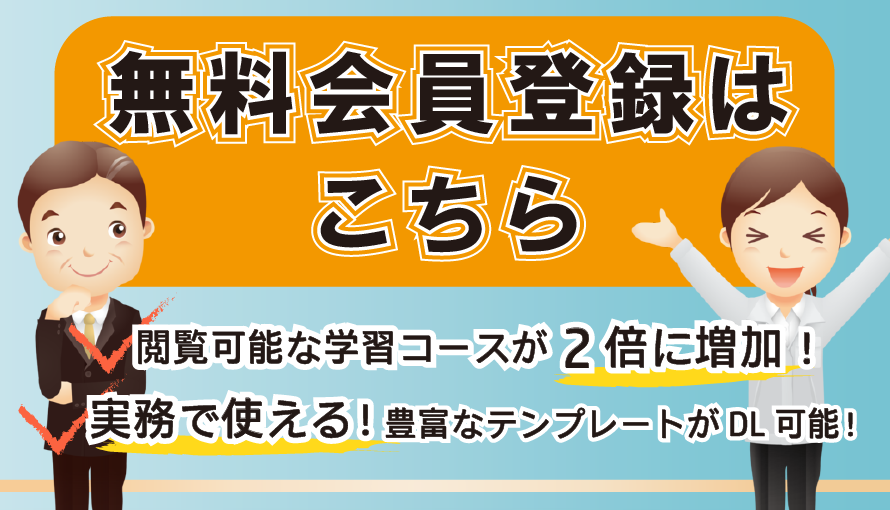
品質のつくり込みのプロセスをレベルアップするPDCAサイクル
PDCAサイクルは、プロセスをレベルアップするためのサイクル
それでは次に、プロセスをレベルアップするPDCAサイクルについて確認します。
PDCAサイクルとSDCAサイクルはご存知ですか?PDCAサイクルは知っているものの、SDCAサイクルは聞いたことがない方もいるのではないでしょうか。
まずは、PDCAサイクルは、次の4つのサイクルを継続的に回していく考え方です。
Plan:計画
目標を決め、それを達成するために必要な計画を立案します。
Do:実行
立案した計画を実行します。
Check:評価
目標に対する進捗を確認し評価・見直しを行ないます。
Action:処置・改善
評価・見直しした内容に基づき、適切な処置を行ないます。
このようなPDCAサイクルを回しながら改善を行なっていくことが、良い品質の製品やサービスを生むプロセスをレベルアップすることに繋がります。品質の水準をレベルアップするために、PDCAサイクルを回す必要があると覚えておきましょう。
成果を定着させるSDCAサイクル
標準化により成果を定着させる!
それでは次に、成果を定着させるSDCAサイクルについて確認しましょう。
SDCAサイクルでは、Planの部分が、Standardizeに変わります。Standardizeは、標準化のことです。
誰でもいつでも同じ方法で作業や業務を行なうことが出来る仕組みをつくることを指します。
標準化により成果を定着させるために、しっかりとSDCAサイクルを回し、確実な管理を行なっていくことが必要不可欠であると覚えておきましょう。
改善と管理の両輪を回していくことが必要
以上のように、品質管理においては、改善と管理の両輪を回していくことが必要です。
改善においては、PDCAサイクルを回しながら、ものづくりのプロセスを改善し、品質水準をレベルアップする。
維持管理においては、改善した内容が定着するように、SDCAサイクルで標準化を行ない、良いプロセスを維持管理する。
このような位置付けで、継続的な改善と管理を行なっていき、継続的な品質レベルの向上を図っていくことが大切となるのです。
あなたの職場では、一度改善したことがいつの間にか後戻りしてしまっていませんか?改善だけではなく、維持管理のサイクルを回す必要性をしっかりと認識するようにしましょう。
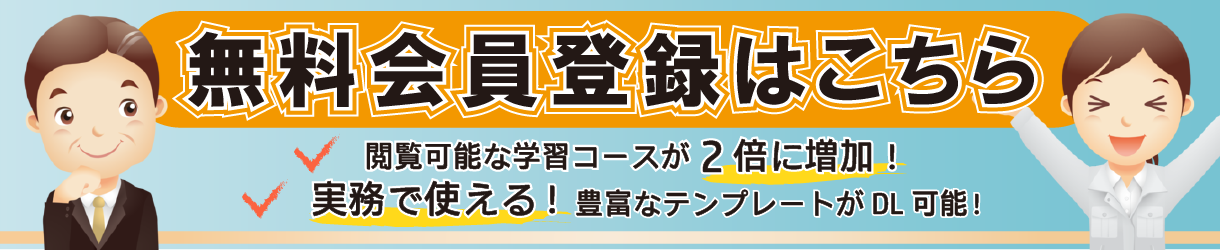
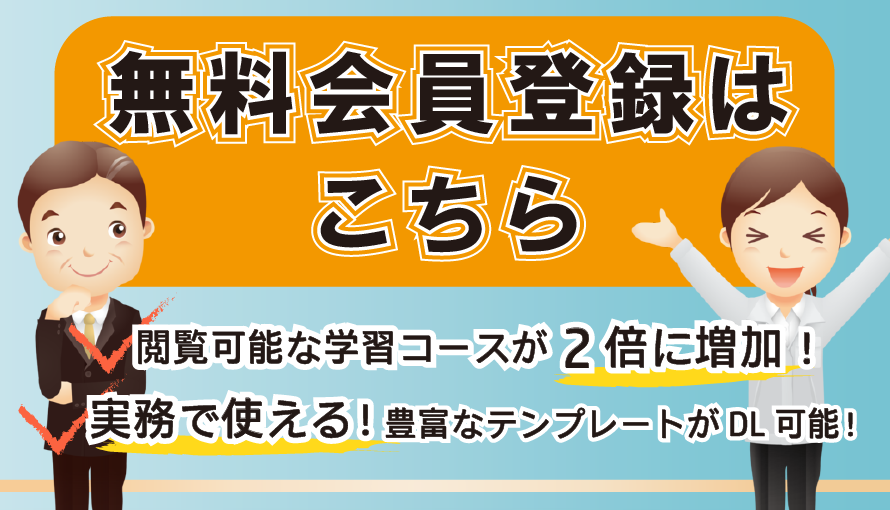
重点指向の考え方
重点指向とは
効果の大きいものにターゲットを絞る
まずは、重点指向とは何か確認しましょう。
重点指向とは、目標を達成するために、結果に及ぼす影響を調査・予測し、効果が大きく優先順位が高いものを重点的に取り組むことを指します。
品質等の改善活動を行なう際、全ての問題に対して満遍なく取り組むことは効率的ではありません。あれもやりたい、これもやりたい、というように、全てのことに取り組もうとして、結局全てが中途半端になってしまったことはありませんか?あるいは、時間を掛けて取り組み改善されたものの、結果的に職場として大きな成果にはならなかったということはありませんか?
改善活動においては、限られた経営資源である人、モノ、金、時間を最大限有効に活用しなければなりません。
そのためにも、「優先順位」を明確にする必要があります。では、どうやって優先順位を付けていったらよいのでしょうか?
一般的には、効果の大きいものにターゲットを絞って改善し、費用対効果を最大にする、「重点指向」という考え方で優先順位を付けて改善を進めていくことが大切です。
重点指向では、同じ費用(労力)を掛けるのであれば、全体の問題の中で大きな問題を優先的に行った方が経済的であると考えて取組みを進めます。言われてみれば当然ではありますが、意外と出来ていないのが、この重点指向なのです。
重点指向で取り組みを進めていくことで、部分最適ではなく全体最適な視点で取り組みが可能となるのです。
意外と出来ていない重点指向
例えば、チームメンバーで集まり、改善テーマを選定する場面をイメージしてみましょう。
あるベテラン社員Aさんが、「最近、トラブルが多いX設備の長時間停止を対策しよう!」と発言したとします。ベテランのAさんが言っているから間違いないだろうと考えテーマを決めます。
しかし、関係者総出で取組みを進め、たしかにトラブルは改善されたものの、本来の大目的である生産性の向上には繋がらなかった、というケースは意外に多いものです。重点指向の意味が分かっており、全体に対して効果の大きいものを選定していたら、このような結果にはなりませんよね。
あなたの職場でこのようなことはありませんか?当たり前のようで意外と出来ていないことが多い、それが重点指向なのです。
重点指向のポイント
優先順位を決める3つの視点
限られた経営資源(人、モノ、金、時間)を最大限有効に活用するためには何をしたらよいのでしょうか。それは「優先順位」を明確化です。では、どうやって優先順位を付けていったらよいのでしょうか?
重点指向で仕事や改善を進めるには、上位方針に対する自分の業務・役割を理解し、結果に大きな影響を与える要素を見極めることが大切です。優先順位を決める際には、次の3つの視点を押さえておくようにしましょう。
まずは、緊急度です。
直ぐに対策を取る必要性があるかどうか、早急に対策しなかった場合に発生する不具合とその影響の大きさや、すぐに対策しなかった場合に起こる結果の深刻さから判断をしていきます。
次に、影響度と重要度です。
問題が影響を及ぼす範囲の大きさを確認します。例えば、その問題を対策しなかった場合に、小さい範囲で済むのか、あるいは会社全体に影響してしまうのか等から判断します。
最後に、拡大傾向です。
その問題を放置することで、どれだけ問題が大きくなるリスクがあるのかを確認します。現在の傾向だけでなく、過去も含めたデータの経過から判断をします。
これらの3つの視点を踏まえて優先順位を決めることが基本となります。
優先順位を明確にして進めよう
物事を効率的に進めていくためには、効果の大きいものにターゲットを絞って改善し、費用対効果を最大にする、「重点指向」という考え方で優先順位を付けて改善を進めていくことが不可欠な要素となります。
重点指向では、同じ費用(労力)を掛けるのであれば、全体の問題の中で大きな問題を優先的に行った方が経済的であると考えるのです。
重点指向の代表「パレート図」
どんな問題を優先的に改善すべきか見える化する
それでは次に、重点指向の代表である、「パレート図」について確認しましょう。
どんな問題を優先的に改善すべきか見える化するツール、それがパレート図です。パレート図とは、問題となるデータを要因別等に層別し、大きい順に棒グラフで並べ、さらに、その項目を足し合わせて累積折れ線グラフを描いた、2種類の組み合わせからなるグラフのことを指します。
ここに示すグラフのように、不具合件数を大きい順に表したい場合などに活用されます。80:20の法則と言われるように、全体件数の80%は、20%の項目が占めていることが多々あります。それを見える化し、効果の大きい項目を浮かび上がらせてくれるツールが、このパレート図なのです。
よく活用するグラフですので、覚えておくようにしましょう。
ABCランクを決め、Aランクから優先的に取り組む
実務においては、このようなパレート図を描き、全体に占める割合が大きいものをAランク、中くらいのものをBランク、小さいものをCランクと明確化します。
そして、Aランクを優先的に取り組み、少ない工数で最大の効果を発揮できるようなアプローチを取ることが成功の秘訣です。
なお、Bランクは、Aランクで取り組めるものがどうしてもない場合や、Aランクだけでは目標に達しない場合にのみ取り組み対象に含めます。
Cランクに関しては、基本的には無視をして、取り組み対象にはしない、といったようにメリハリを付けて進めることがポイントとなります。
目先の事に囚われない取組みを
品質を効率的に向上させるには、重点指向が大切
それでは、繰り返しになりますが、目先の事に囚われない取組みの必要性について再確認します。
ここまでで確認したように、品質を効率的に向上させるには、重点指向が大切です。
目の前で起きている問題は、全体として見ると必ずしも重要な問題とは限りません。
それよりも、今はまだ見えていない事の方が、重要な問題が潜んでいる可能性もあるのです。その重要な問題を客観的に見える化するためにも、パレート図等のツールを用いて表現をすることが重要です。つまり、
- 問題をパレート図等を使い、数値で客観的に見える化すること
- 重点指向で優先順位を明確にすること
- 限られた資源を有効に活用した問題解決をすること
これらを忘れずに取り組みを進めていくようにしましょう。
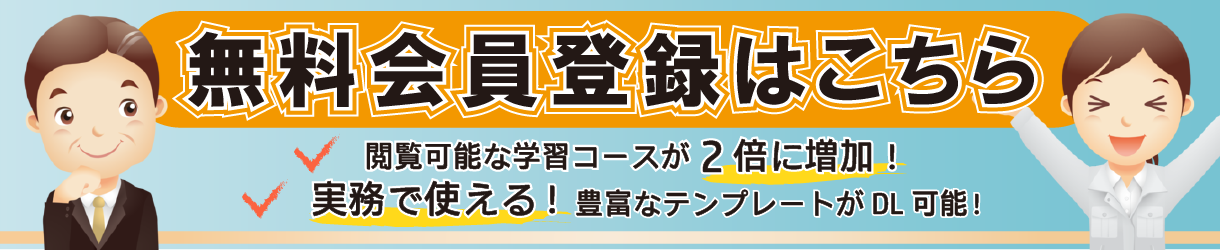
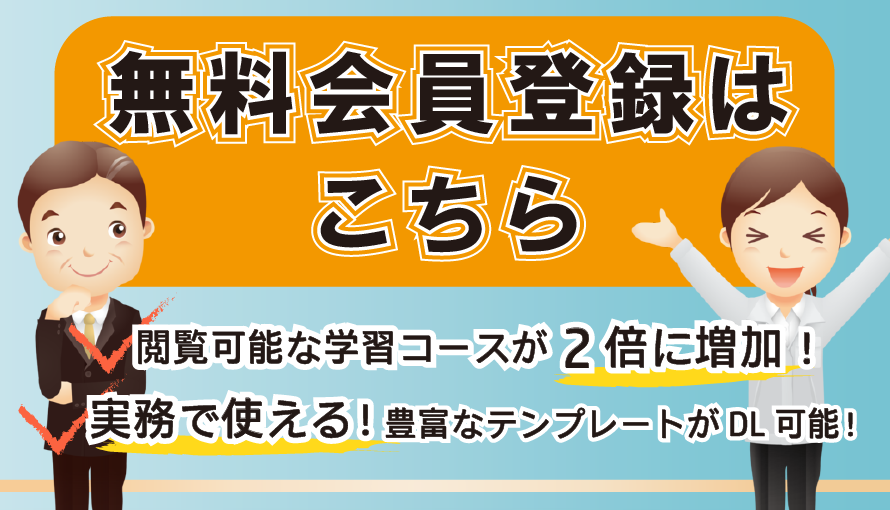
品質改善、重点指向、維持管理(PDCAサイクルとSDCAサイクル)のまとめ
以上で学んだことをまとめてみましょう。
品質改善とは?PDCAサイクル・SDCAサイクルとは?重点指向とは?
- 改善だけでは後戻りしてしまう。管理だけでは水準の向上にはならないため、改善と管理は両輪を回していかなければならない
- PDCAサイクルとは、Plan:計画、Do:実行、Check:評価、Action:処置改善のサイクルのこと。品質水準を向上するサイクル
- SDCAサイクルとは、PDCAサイクルのPlanの部分が、Standardize:標準化に変わったもの。改善したことを確実に管理していくための、品質の維持管理のサイクル
- 重点指向の考え方により、全体の中で効果の大きなものを優先できるため成果を上げ易く効率的
- 優先順位を決める3つの視点は、緊急度、影響度・重要度、拡大傾向
- パレート図とは、どんな問題を優先的に改善すべきか見える化するツール
いかがでしたか?品質改善、PDCAサイクル・SDCAサイクル、重点指向の考え方は理解できましたか?
重点指向の考え方で品質改善のPDCAサイクルを回し、後戻りしないようにSDCAサイクルで維持管理することで、より良い製品づくりを目指していきましょう!
品質管理について学ぶ!学習コースのご紹介
カイゼンベースの学習コースでは、品質管理に関する具体的な内容を動画や理解度テストにより学習することが可能です。詳細の学習や実践でのご活用をご検討の方は、是非ご活用ください。
学習コース「k1-12:アニメで学ぶ品質管理と品質改善活動」
品質管理は、ものづくりを行う企業を初めとして、あらゆる会社で必要不可欠な取り組みです。本コースでは、自工程保証、標準化など、品質管理において欠くことのできない考え方を学習します。
学習コースの詳細
Lesson1:品質優先の考え方(7:53)
Lesson2:後工程はお客様(自工程保証の考え方)(9:08)
Lesson3:プロセス管理と源流管理(7:51)
Lesson4:標準化の考え方(8:52)
Lesson5:重点指向(8:02)
Lesson6:品質改善と維持管理の考え方(7:20)
「Lesson1:品質優先の考え方」の動画はどなたでもご視聴頂けます。
「Lesson2:後工程はお客様(自工程保証の考え方)」の動画は無料会員登録を行うことでご視聴が可能になります。
資料請求はこちらから
サービス紹介資料・価格表を無料でダウンロードできます。お気軽にお問い合わせください。

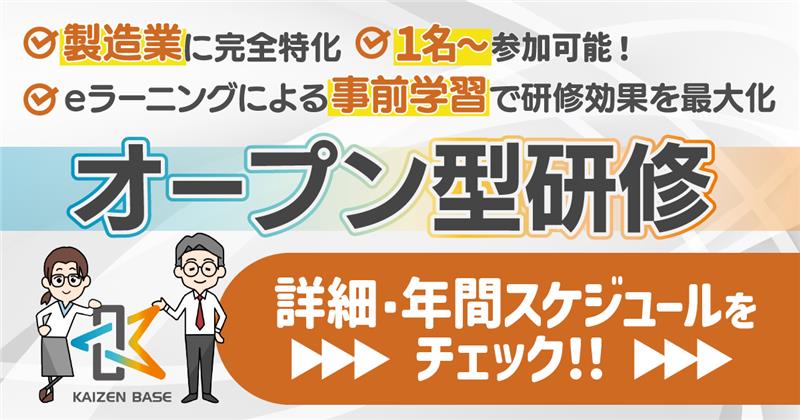
関連学習動画
-
k2-04
アニメで学ぶ5S活動~5Sの概要と整理整頓編~
有料サービス限定
3:5Sによる効率の向上
受講対象者
現場部門, 間接部門, 新人, 一般, 主任・班長クラス, 係長クラス, 課長クラス- カリキュラム構成
-
- 5Sによる効率の向上とは
- 整理整頓ゲームで効果を確認
- モノ探しの年間ロスコスト
- まとめ
-
k2-23
アニメで学ぶトヨタ生産方式~中級編:自工程完結と継続的な品質改善~
公開講座
Lesson1:継続的品質改善に必要なこと(前編)
受講対象者
係長- カリキュラム構成
-
- はじめに
- 品質方針とは
- プロセス管理と源流管理
- まとめ
-
k2-01
アニメで学ぶトヨタ生産方式~入門編~
有料サービス限定
5:工程の流れ化とは?
受講対象者
現場部門, 間接部門, 一般, 主任・班長クラス, 係長クラス, 課長クラス- カリキュラム構成
-
- 工程の流れ化とは
- 工程を「細く速い流れでスムーズに」流すとは
- 1個流し生産と小ロット生産
- 整流化とは
- まとめ
-
k2-19
アニメで学ぶIE実践編~応用手法 Part2~
無料会員限定
Lesson2:ラインバランス分析の進め方と基本パターン
受講対象者
全部門(管理職)- カリキュラム構成
-
- はじめに
- ラインバランス分析の進め方
- ラインバランス改善の基本パターン
- ラインバランス改善の事例
- まとめ
-
k2-02
アニメで学ぶトヨタ生産方式~初級編~
有料サービス限定
3:人の“働き”と“動き”の違い
受講対象者
生産部門全般 一般- カリキュラム構成
-
- 「働き」と「動き」の違い
- 「動き」を「働き」に変えていく
- 付加価値を付けるとは
- 付加価値かどうかの判断方法
- まとめ
-
k2-17
アニメで学ぶIE実践編~運搬分析 Part2~
無料会員限定
Lesson2:運搬活性分析図を使った改善事例
受講対象者
全部門(管理職)- カリキュラム構成
-
- はじめに
- 事例(改善前)
- 事例(改善後)
- まとめ