5S活動で現場が変わる!成功事例に学ぶ「進め方」と「アイデア」、「目標例」
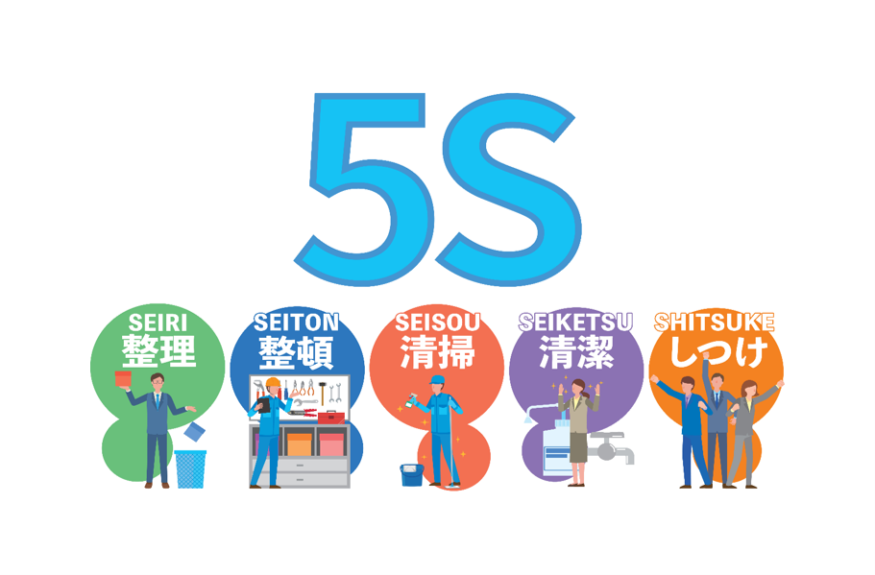
目次
はじめに:5S活動が生む「強い現場」とは
製造業の生産現場では、「探し物に時間がかかる」「道具や部品がどこにあるか分からない」「ムダやロスが多くて困っている」など、多くの課題が存在します。こうした課題は日々の業務の妨げになるだけでなく、最終的にはコスト増や納期遅れ、品質トラブルといった問題につながりかねません。
そこで重要になってくるのが、5S活動です。
5S活動とは、生産性・品質・安全など、あらゆる面で「強い現場」をつくるために必要な土台をつくる活動と言われます。5Sは業務の土台であり、カイゼンを進めるための第一歩でもあるため、トヨタ生産方式をはじめとする世界中の製造現場でも広く導入されています。
本記事では、5S活動とは何か、進め方・アイデア・事例・目標例などを網羅的に解説します。
5S活動とは?──整理・整頓・清掃・清潔・躾
「5S活動とは」、整理(Seiri)・整頓(Seiton)・清掃(Seisou)・清潔(Seiketsu)・躾(Shitsuke)の頭文字Sを取ったものを指します。現場を効率的・安全に維持管理するための基本的な仕組みです。もともとは日本独自の取り組みでしたが、海外でも「5S (Five S)」として注目され、工場のみならず病院やオフィスでも応用されています。
- 整理(Seiri,英語では「Sorting」)
必要なものと不要なものを明確に区分し、不要なものを排除すること。倉庫にある長年使っていない部品や、机の引き出しに眠る古い書類などを徹底して取り除くのが整理のポイントです。 - 整頓(Seiton,英語では「Setting-in-order」)
必要なものを必要な時に誰でもすぐ使えるよう配置・表示すること。3定(定品・定位・定量)で管理することで、取り出しやすさと戻しやすさを確保し、探し物をゼロに近づけます。 - 清掃(Seisou,英語では「Shining」)
職場や設備をきれいに保ち、同時に異常や不具合の早期発見を行うこと。単なる掃除作業ではなく、「清掃+点検」という視点で故障や不良品の発生を未然に防ぐ狙いがあります。 - 清潔(Seiketsu,英語では「Standardizing」)
上記3S(整理・整頓・清掃)を維持し続けること。誰が見ても常に清潔な状態を保つためには、ルール化・標準化が不可欠です。たとえば清掃当番表や5Sチェックリストの整備、定期巡回などが含まれます。 - 躾(Shitsuke,英語では「Sustaining」)
いわゆる「しつけ」です。決めたルールを守り、良い習慣を自律的に定着させること。5Sを現場の文化として根付かせる最終段階であり、ここまで達すると管理者がいなくても5Sが自然に続いていきます。
この5Sのステップは、現場カイゼンの基盤です。「仕事の邪魔になる不要物やムダ・ムラ・ムリをなくし、モノと人がスムーズに動ける環境をつくる」ことが、5S活動の根幹といえます。
5S活動の目的と効果
5S活動の本当の狙い
「5Sはただの掃除」と思われがちですが、本質は職場を最適化するための仕組みづくりにあります。単に物がきれいに揃っているだけではなく、社員の意識改革や組織の風土醸成まで含めてトータルで改善を図るのが5S活動の目的です。「儲け続ける強い会社は5Sが定着している」といわれるように、5Sを徹底することでムダの排除・士気の向上・安全性の確保など、経営上のあらゆるメリットが得られます。
5S活動の効果
5Sがしっかり機能すると、以下のような効果が期待できます。
- 生産性向上
整理整頓が行き届いた現場では、探し物の時間が激減します。部品・工具がすぐ取り出せるよう定位置管理すれば、段取り時間も短くなり、結果として生産性が向上します。 - 品質管理の安定
清掃しやすい職場は異常や不具合を早期発見しやすくなります。切粉の詰まり、油漏れ、異物混入といったトラブルにもいち早く気づけるため、不良やクレームの発生を未然に防げます。 - 安全確保
通路が明確になり、床や装置周りもきれいに整えられるため、転倒事故や物損事故、挟まれ事故のリスクが低減します。「5S不足は労災の元」と言われるほど、安全面との関係は深いです。 - コスト削減
不要在庫や重複発注が減り、故障リスクも低減されるため、資材費・設備保全費など様々なコストが削減されます。 - 社員のモチベーション向上
整然とした職場で働けることは、作業者にとってストレス軽減や意欲向上につながります。さらに、チームで改善に取り組む過程でコミュニケーションが活性化し、企業風土を大きく変える力になります。
このように、「5Sは全ての現場カイゼンの基礎」であり、強く儲け続ける企業文化をつくり、継続的なカイゼン活動を推進するための土台づくりなのです。
5S活動の進め方(導入から定着まで)
ここからは「5S活動 進め方」のステップを具体的に見ていきます。大きく分けると、計画(Plan)→実行(Do)→評価(Check)→改善(Act)というPDCAの流れです。
ステップ1:目的・方針の共有(Plan)
• 経営層からのメッセージ発信
なぜ5Sが必要なのか、何を目標にするのかをトップが明言します。たとえば「納期遅延ゼロを目指すために5Sを徹底する」「新工場の稼働に合わせて5Sレベルを上げる」などが該当します。
• 推進体制の確立
5S委員会やプロジェクトチームなどを立ち上げ、責任者やメンバーを明確にします。組織的に取り組むことで、部分最適に陥らないようにする狙いがあります。
ステップ2:現状把握と問題の見える化(Do:準備段階)
• 現場巡回と写真撮影
倉庫や作業エリアなど、散らかった場所や不要物が多い箇所をリストアップし、写真に収めます。後々のビフォーアフター比較にも役立ちます。
• 赤札作戦の計画
不要物に赤札を貼って洗い出す「赤札作戦」をどう実施するか検討します。実施日程や対象エリアの優先順位を決めましょう。
ステップ3:5S実行(Do:実践段階)
• 整理(Seiri)の徹底
不要物を思い切って排除します。廃棄・売却・移動などで職場から余計なものをなくします。
• 整頓(Seiton)の仕組みづくり
3定(定位置・定品・定量)を決め、表示ラベルやマーキングを活用して誰でも分かるようにします。置き場管理のルールを作り、全員に周知します。
• 清掃(Seisou)で異常を見つける
掃除をしながら設備のチェックを行い、不具合や異常の早期発見に努めます。清掃手順を標準化し、清掃当番表を作るなどして日常業務に組み込みます。
• 清潔(Seiketsu)で状態維持
ここまでの取り組みを守り続けるために、清潔保持のルールや5Sチェック表を作成します。巡回パトロールや月1回の評価会議などを取り入れ、乱れが発生していないかチェックを継続します。
• 躾(Shitsuke)として定着
5Sルールを守れなかった場合、すぐに注意・指導する仕組みを整えます。朝礼や社内報で5S事例を共有し、全員が主体的に改善を意識する企業風土をつくります。
ステップ4:定期チェックと標準化(Check)
• 5Sチェックリストで点検
たとえば「必要な物以外は置かれていないか」「表示が正しく機能しているか」など、項目を可視化して採点します。客観性を高めるために部署間で交互に点検する方法も有効です。
• 結果の見える化
採点結果を社内の発表会や掲示板、イントラネットで公開し、優秀部署を表彰します。また、改善が遅れている部署をサポートする流れを作ります。
ステップ5:振り返りと改善(Act)
• 問題点の洗い出しと対策
チェックリストで低得点だった項目を分析し、「なぜうまくいかなかったのか」を追究します。必要があればルール自体を変更するなど柔軟に対処します。
• 継続的なPDCA
5Sは一度やって終わりではありません。さらに職場を良くするため、PDCAサイクルを何度も回してアップデートし続けることが大切です。
5S活動を成功させるためのポイント
経営層のコミットメント
5S活動は「現場の従業員1人1人が行うもの」と思われがちですが、実はトップの旗振りが最も重要です。社長や工場長が自ら現場を回り、一緒に片付けを行う姿勢を見せることで、社員が「これは本気の取り組みだ」と認識します。トップが動かないと、5Sは形だけで終わり、すぐに元の状態へ逆戻りしやすくなります。
全員参加と意識改革
5Sは特定の有志だけでは定着しません。「自分の職場は自分で良くする」という意識づけが不可欠です。朝礼や研修の場を活用し、「ムダ・ムラ・ムリを見逃さない」「ルールを守らないと迷惑がかかる」といった意識を全社員に植え付けます。特に新入社員やパートの方にも分かりやすく説明し、誰でも関われる状態をつくることが大切です。
定期的な仕掛けでマンネリを防ぐ
人はすぐに「慣れ」や「飽き」に陥ります。そこで、5Sコンテスト(各部署のBefore/Afterの好事例を競ったり、施策や状況が優れている職場を表彰したりする取り組み)や標語・スローガン募集、5S月間の設定などの仕掛けを用意すると良いでしょう。楽しさや競争要素を取り入れることで、継続意欲が高まり、社員同士のコミュニケーションも促進されます。
形式的な5Sで終わらせない
「とりあえず物を隠して見た目だけ整える」「チェックリストに形だけ○を付けて終わり」というような表面的な5Sには要注意です。5S本来の目的は現場の問題を可視化し、継続的に改善することにあります。表面的な片付けに満足せず、「なぜ散らかるのか」「なぜ紛失するのか」を突き詰めて対策する姿勢を忘れないようにしましょう。
他の改善手法との連携
5Sは現場改善のスタートラインです。ここから発展してTPM(Total Productive Maintenance/Management)や品質管理、IE手法、さらにはDXとの連携など、さまざまな改善活動へとつなげることができます。いずれも5Sがしっかりしている職場ほど、スムーズに導入・定着が進む傾向があります。
5S活動アイデア:職場が楽しく変わる工夫集
ここでは「5S活動のアイデア」をいくつかピックアップします。取り組みを「楽しく、わかりやすく、続けやすく」する工夫を加えると、マンネリを防ぎ成果も出やすくなります。
- シャドウボード(姿置き)
工具や部品の形をボードに描いておき、置く場所を可視化する方法です。新人でも一目で正しい位置が分かり、物の紛失・探し物を防ぎます。 - ビフォーアフター写真の共有
Before/Afterの写真を社内SNSや掲示板に貼り出すと、改善効果が目に見えて分かりやすいです。「こんなに職場がスッキリした!」という成功体験を全員で共有しましょう。 - 5Sチェックリストの点数でライバルセッティング
部署ごとに5Sのチェック項目をスコア化し、毎月の平均点を競う仕組みを導入します。上位部署には表彰やご褒美を出すとモチベーションアップに効果的です。 - 標語・スローガンの活用
「5S運動 つなげて広げて みんなの輪」「続けよう 今日の5S 明日の改善」など、覚えやすいフレーズを職場に掲示します。社内でスローガンを公募すれば全員参加が促進されます。 - 5Sデーの設定
週に1回、または月に1度、決まった日に全員で5Sを実施するイベントを設定します。例えば「毎週金曜の15時~15時半は5Sタイム!」などとすれば、習慣化しやすくなります。
5S活動 事例紹介:成功例から学ぶ
5S活動をよりイメージしやすくするために、具体的な事例をいくつか取り上げます。
在庫管理の改善
ある製造工場では、消耗品の保管場所があいまいなため在庫が過剰になったり、逆に欠品が見つからずラインが止まったりすることもありました。そこで整理(不要在庫の一斉処分)を実施し、在庫ボックスに数量表示・写真ラベルを貼って整頓を徹底。同時に「かんばん方式」も取り入れて使用量を自動的に補充する仕組みを導入したところ、過剰在庫を大幅に削減できただけでなく、ラインストップゼロを達成しました。
工具置き場の整頓
金属加工を行う工場では、複数の作業台で工具がバラバラに使われており、紛失・探し物が日常茶飯事でした。そこで「工具ボード」を姿置き形式(下図)で製作し、名称と数量を明示したうえで定位置を決めました。作業者が戻しやすくなり、1日に数十分かかっていた工具探しの時間がほぼゼロになったとのことです。
清掃で品質を向上
ある食品工場では、床や設備の汚れが製品不良や異物混入につながるリスクが高いことが問題になっており、実際に少なからずクレームも発生していました。そこでこの会社では、3S(整理・整頓・清掃)を集中的に実施することにしました。具体的には、週に一度のピカピカ作戦で全員が担当エリアの徹底的な清掃を行いました。異物混入が激減しただけでなく、トラブルに対するリスク感度が高まり、品質意識が社員全体に定着しました。
5S活動 目標例:成果を引き出す目標設定とは
「5S活動がどのくらい進んだのかは、単に「きれいになった」という感覚では測ることができません。具体的な達成指標を作り、進捗をモニタリングすることが大切です。たとえば以下のような目標を参考にすることをおすすめします。
- 作業効率:物探し時間50%削減
改善前の平均物探し時間を把握しておき、一定期間後に再計測するなどにより測ることが可能です。 - 在庫削減:死蔵在庫金額80%低減
倉庫の保管品リスト等を作成し、使用予定のない品は売却・廃棄。定期的に棚卸しして残数を確認します。死蔵在庫とは、例えば1年以上使用していない在庫のことを指します(期間は会社により異なります)。死蔵在庫はスペースを占有するだけで価値を生み出しません。この死蔵在庫を定期的に確認し削減する仕組みをつくることで在庫削減に繋げます。 - 安全:ヒヤリハット件数を50%削減
5Sパトロールや日常点検で危険箇所をヒヤリハットとして提出、件数をカウントします。提出されたヒヤリハットの改善を繰り返し、ヒヤリハット自体を減らしていきます。 - 品質改善:不良率50%低減
清掃点検を通じて異物混入や設備故障を未然防止し、不良やクレームを削減します。不良率の中で異物混入に関するものを明確化し、清掃実施有無による影響などを数値で分析します。 - 5S定着度:5S定期監査で平均80点以上
監査チェックリストを作り、各部署の平均点をモニタリングします。結果を可視化し、目標達成度を共有していきます。
目標は「10月末までに」「50%改善する」といったように、期限と数値を入れ明確化するのがポイントです。これにより、社員は「どこをどれだけ良くすればいいか」を具体的にイメージしやすくなります。さらに、達成度合いを定期的に評価・見直ししていくことが、PDCAサイクルを回すうえでも効果的です。
よくある質問(FAQ)
Q1. 5S活動は製造業以外でも役立つの?
A. もちろんです。オフィスの書類管理や、病院の器具配置など、あらゆる業界で5Sの考え方は活かすことができます。ポイントは「必要なものを必要な時に取り出せる」「清潔かつ安全を保つ」という基本原理であり、製造業以外でも有効です。
Q2. 5Sを始めてもすぐに職場が乱れます。どうすれば定着する?
A. 「仕組み」づくりと「指導」の両面が大切です。定置管理だけでなく、5Sチェックリストや定期巡回、5S当番などを導入して、乱れを未然に防ぐルールを作ります。また、管理者が巡回時に乱れを発見したら早期に指摘・改善することが効果的です。組織のトップの意志が5S状態と密接に関係していると考えることが大切です。
Q3. 5Sに取り組むメリットを、従業員にどう伝えればいい?
A. 「楽になる」「仕事がスピードアップする」といった個人の利益をアピールすると伝わりやすいです。物探しが減る、ミスが減る、作業がしやすくなるといった、身近な変化を実感させるのがポイントです。
Q4. 5Sとカイゼン(改善)はどう違うの?
A. 5Sはカイゼンの土台にあたります。5Sは「現場を整理・整頓して問題点を発見しやすい環境を作る」ことに焦点があります。5Sが進んでこそ、次なる工程改善や品質管理の手法が効果を発揮します。
Q5. 外部コンサルタントに依頼すべき?
A. 社内でノウハウが全くない場合、専門家の助言を受けるのも選択肢の一つです。ただし最終的には社内の現場力で継続する必要があります。コンサルタントはあくまでやり方を教える役割と捉え、自社のスタッフが主体的に動く仕組みを構築することが大切です。
まとめ:5Sは「現場改善」の第一歩
5S活動は、一見すると地味な「片付け」や「掃除」のように思われがちです。しかし、実際には生産性・品質・安全など、すべての現場力に直結する重要な基盤となります。整理・整頓・清掃・清潔・躾という5つのステップを着実に進め、現場を最適化すれば、多くのムダ・ムラ・ムリが削減され、さらに一歩進んだカイゼンの効果が大きく表れるようになります。
• 5S活動 とは
現場のモノや情報を最適な状態に保ち、問題点を素早く見つけ出して解決する仕組み。
• 5S活動 進め方
計画→準備→実行→チェック→改善というPDCAサイクルで継続する。
• 5S活動 アイデア
姿置きボード、5Sコンテスト、ビフォーアフター共有など、楽しみながら続ける工夫を組み込む。
• 5S活動 事例
倉庫の在庫管理、工具置き場の整頓、食品工場の清掃など、どんな現場でも効果は明確。
• 5S活動 目標例
物探しの時間半減、不良率50%低減、5S定期監査80点以上など、定量的に目標設定すると達成度が高まる。
「5Sは仕事の一部」という意識を持ち、全員参加でコツコツと続けていけば、企業全体の文化や風土も変わっていきます。製造業の社長・工場長・教育担当の皆さまが5Sに本気で取り組むことで、儲け続ける強い会社への道が開かれるはずです。今日からでも始められる5Sこそが、現場改善の第一歩。ぜひ、あなたの工場でも取り組んでみてください。
5S活動について学ぶ!学習コースのご紹介
カイゼンベースの学習コースでは、5S活動に関する具体的な内容を動画や理解度テストにより学習することが可能です。詳細の学習や実践でのご活用をご検討の方は、是非ご活用ください。
学習コースの概要「k2-04:アニメで学ぶ5S活動~5Sの概要と整理整頓編~」
5Sの定義や5Sを行う理由、整理整頓のポイントについて学習するコースです。すべての会社で必要不可欠な5S活動、そのベースとなる知識をしっかりと身に付けます。
学習コースの詳細
Lesson1:5S活動とは~5Sの定義と狙い~(10分)
Lesson2:5Sと安全・品質・ムダの関係(11分)
Lesson3:5Sによる効率の向上(9分)
Lesson4:整理のポイント① 必要不要の基準づくり(10分)
Lesson5:整理のポイント② 不要なモノを増やさない仕組み(8分)
Lesson6:整頓のポイント① 最重要な3定管理(10分)
Lesson7:整頓のポイント② ロケーション管理とその他の仕組み(12分)
「Lesson1:5S活動とは~5Sの定義と狙い~」の動画はどなたでもご視聴頂けます。
「Lesson2:5Sと安全・品質・ムダの関係」の動画は無料会員登録を行うことでご視聴が可能になります。
資料請求はこちらから
サービス紹介資料・価格表を無料でダウンロードできます。お気軽にお問い合わせください。
関連学習動画
-
k2-04
アニメで学ぶ5S活動~5Sの概要と整理整頓編~
無料会員限定
2:5Sと安全・品質・ムダの関係
受講対象者
現場部門, 間接部門, 新人, 一般, 主任・班長クラス, 係長クラス, 課長クラス- カリキュラム構成
-
- 5Sの対象とは
- 5Sは会社で行う全ての仕事に関係
- 5Sはなぜ必要?
- 5Sの効果として当てはまるものは?
- 5Sと安全の関係
- 5Sと品質の密接な関係
- 5S不足により発生する各種のムダ
- まとめ
-
k2-04
アニメで学ぶ5S活動~5Sの概要と整理整頓編~
公開講座
1:5S活動とは~5Sの定義と狙い~
受講対象者
現場部門, 間接部門, 新人, 一般, 主任・班長クラス, 係長クラス, 課長クラス- カリキュラム構成
-
- 5Sの定義とは
- 5S活動の目的
- 5Sが定着している職場の特徴?
- 5S活動において注意すべきこと
- まとめ
-
k2-04
アニメで学ぶ5S活動~5Sの概要と整理整頓編~
有料サービス限定
6:整頓のポイント① 最重要な3定管理
受講対象者
現場部門, 間接部門, 新人, 一般, 主任・班長クラス, 係長クラス, 課長クラス- カリキュラム構成
-
- 整頓の定義とは
- 3定管理とは
- 姿置きによる3定管理の例
- コンビネーションプライヤーとは
- 工具台車の姿置きの事例
- 工具掛けの姿置きの事例
- よくある失敗事例
- まとめ
-
k2-04
アニメで学ぶ5S活動~5Sの概要と整理整頓編~
有料サービス限定
7:整頓のポイント② ロケーション管理とその他の仕組み
受講対象者
現場部門, 間接部門, 新人, 一般, 主任・班長クラス, 係長クラス, 課長クラス- カリキュラム構成
-
- ロケーション管理とは
- ロケーション管理の必要条件
- 保管棚のロケーション管理の例
- 大物置き場のロケーション管理の例
- あるべき姿カードを使った3定管理
- 立て看板を活用した置き場管理
- 資材置き場における立て看板の悪い活用事例
- 整頓の仕組み
- まとめ
-
k2-04
アニメで学ぶ5S活動~5Sの概要と整理整頓編~
有料サービス限定
3:5Sによる効率の向上
受講対象者
現場部門, 間接部門, 新人, 一般, 主任・班長クラス, 係長クラス, 課長クラス- カリキュラム構成
-
- 5Sによる効率の向上とは
- 整理整頓ゲームで効果を確認
- モノ探しの年間ロスコスト
- まとめ
-
k2-04
アニメで学ぶ5S活動~5Sの概要と整理整頓編~
有料サービス限定
5:整理のポイント② 不要なモノを増やさない仕組み
受講対象者
現場部門, 間接部門, 新人, 一般, 主任・班長クラス, 係長クラス, 課長クラス- カリキュラム構成
-
- 定期的なパトロール
- 赤札作戦
- 赤札の参考例
- 黄札の参考例
- 赤札作戦の実施事例
- まとめ