セル生産方式とは?セル生産の特徴や導入を成功させるために必要な仕組みを解説
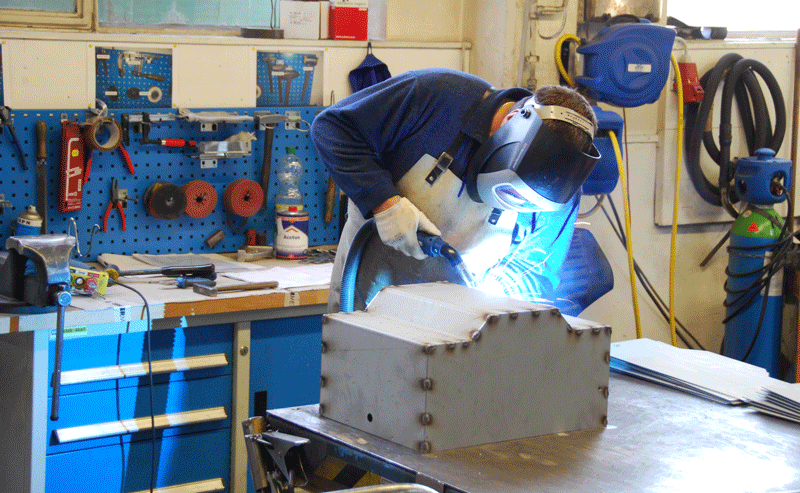
.png)
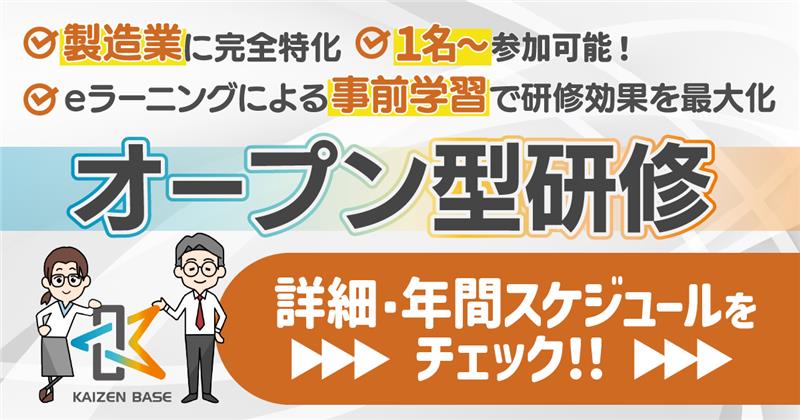
目次
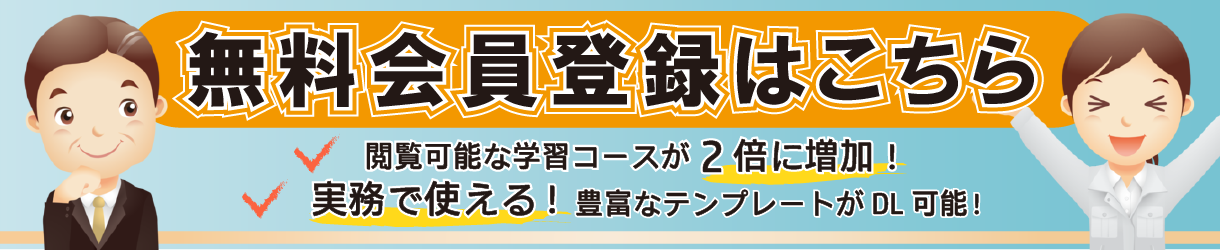
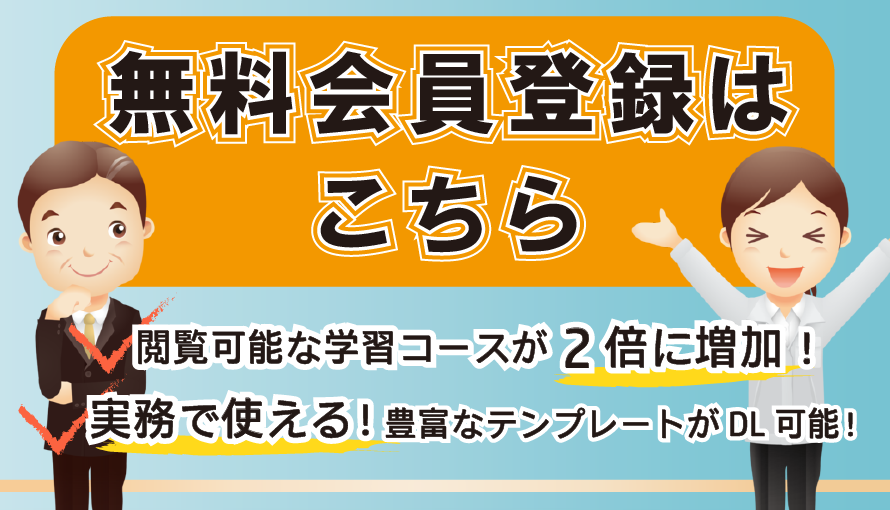
セル生産方式とは何か?セル生産の特徴や導入を成功させるために必要な仕組みを解説
本ページでは、代表的な生産方式の1つであるセル生産方式について概要を解説しています。セル生産の特徴や、メリットと課題、セル生産を成功させるための仕組み等について学習しましょう。
セル生産方式の定義
セル生産方式は、「1人あるいは数人の作業者が、ひとつの製品を造り上げる自己完結性の高い生産方式」です。
セル生産方式は、次のようなメリットを持つ生産方式となります。
- 自分で造った商品という意識が芽生える(責任感が向上する)
- そのことにより、不良が低減する
- モチベーションが向上しやすい
- 改善提案が活性化する
セルの一般的な形態
セル生産方式には、次の4つの一般的な形態を取ります。
- 1人方式セル
- 分業方式セル
- 巡回方式セル
- インライン方式セル
それぞれの特徴を確認してみましょう。
1人方式セル
1つ目の形態は、「1人方式セル」です。
セル生産は、この1人方式のセルが基本形となります。
1人セルは、編成効率100%となることが大きなメリットです。
ただし、組立点数が多い場合は高い作業習熟度が要求されることや、生産量が多い場合はセルが異常に増えてしまうこと等、課題もあります。
分業方式セル
2つ目の形態は、「分業方式セル」です。
生産量が多い場合や、多能工の育成が十分に進んでいない場合、組立部品点数が極めて多い場合等に採用されることが多いセルの形態です。
分業方式セルでは、編成効率と作業者間の仕掛在庫数を常に意識する必要があります。
また、1つのセルの人数が多くなってしまうと、コンベアラインと同様に、ラインバランスを取ることが難しくなってしまうことにも留意しなければなりません。
巡回方式セル
3つ目の形態は、「巡回方式セル」です。
巡回方式セルは、1人方式セルの発展形になり、巡回する作業者の人数を増減させることで生産量を調整することが可能です。基本的には、1つの完成品を1人で造ります。複数人で順番に同じ作業を行ないますので、兎(うさぎ)追い方式とも呼ばれます。
なお、巡回セル方式では、作業者の人数が多くなると作業スピード差により、前後の作業者が詰まってしまい「手待ち」が生まれ、停滞ロスが発生することがあります。
また、あまりに中型・大型組立製品になると、適用が難しいあるいは適用出来ないこともあると覚えておきましょう。
インライン方式セル
3つ目の形態は、「インライン方式セル」です。
インライン方式セルは、コンベア生産とセル生産の中間型となります。
コンベア生産から移行しやすいという特徴がありますが、工程間の同期を取るのが難しく編成効率も低下しやすいことに注意が必要です。
形にこだわらなくてOK!
セルは日々進化させていかなければいけないものです。
必ずこの形でないといけない等の制約はありません。
つまり、形にこだわる必要は無いので、色々なアレンジや工夫を織り込みながら、「自社流のセル」を構築していくようにしましょう!
コンベア生産の問題点とセル生産
コンベア生産は遅い人にスピードを合わせる
それでは、セル生産方式の特徴を理解するために、コンベア生産方式の問題点とセル生産における解決策ついて確認します。
コンベア生産方式の問題点の1つ目は、「最も作業の遅い人に全員が影響されてしまう」ことです。
コンベア生産は、多くの場合、大人数での作業編成となりますが、「1人が遅いと全員がスピードを落とさなければ」いけません。
その点、セル生産では、1人~数人の作業である為、その影響が小さくなるのです。例えば、1名が新人だったとしても、作業分担を少し変更し、他の作業者と作業時間を平準化することで、全体のスピード低下を和らげることが可能となります。
コンベア生産はラインバランスが取りにくい
コンベア生産方式の問題点の2つ目は、「作業者が多いとラインバランスが取りにくい」ことです。
大人数のラインにおいて、ラインバランスを完全に取るのは至難の業です。
一方、セル生産では、1人~数人の作業である為、ラインバランスを取ることが比較的容易となります。
ただし、コンベアラインでは、一度作業をつくり込んでしまえば、コンベアのスピードがペースメーカーとなるため、サイクルタイムは安定しやすいというメリットがあることも忘れてはいけません。セル生産では、コンベアというペースメーカーが無いため、後述するタクトタイム規制などの仕組みが必要不可欠です。
コンベア生産は切り替えロスが出易く、初期投資が大きい
コンベア生産方式の問題点の3つ目は、「多品種職場では、品種切替時間が長くなりロスが生まれやすい」ことです。
セル生産は大型設備ではないため、小規模な段取り替え程度でロスを小さくすることが可能です。
コンベア生産方式の問題点の4つ目は、「初期投資額が大きくなる」ことです。
セル生産では、コンベアラインに比べて投資額を抑えることができます。
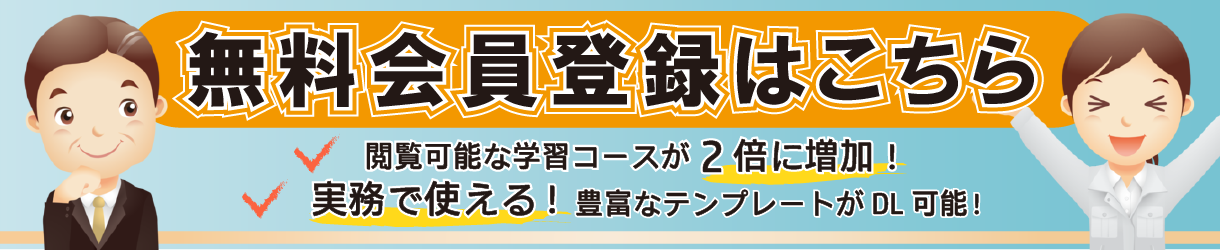
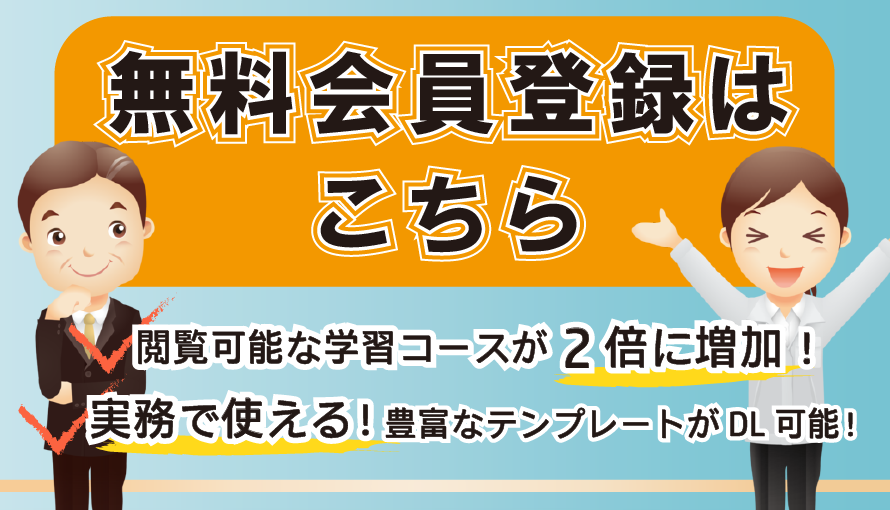
セル生産のメリット
セル生産における様々なメリット
セル生産のメリットをまとめると下記のようになります。
- 生産量・品種の変動に対応しやすい
- 生産性の向上が推進しやすいい
- 改善の効果がすぐに反映されるい
- 品質への意識が高まる(不良率減)い
- 作業者の責任感が高まるい
- 仕掛在庫を減らしやすいい
- 製造リードタイムが短縮されるい
- 設備投資が少なくて済むい
セル生産には、こんなに沢山のメリットがあるんですね!
セル生産の課題
ただし、メリットだけではなく、いくつか課題もあります。
その中でのセル生産の一番の課題は、「作業者のモチベーションによって、生産性が低下する」可能性があることです。
上述したようにセル生産は、コンベア生産とは異なり、ペースメーカーとなるものがありません。従って、作業者の意識や体調によって、生産性が良かったり悪かったりしてしまうのです。
セル生産方式も万能ではない!
以上のように、セル生産方式も万能ではありません。
従って、「ただセルの屋台を導入するだけ」では、メリットは得られないことを十分に認識しておかなければなりません。
そして、セル生産方式を導入する際には、「セルの屋台の設置に加え、各種の規制や仕組みを構築する」ことにより、セル生産方式が有する課題に対して、解決策を用意しておくようにしましょう。
セル生産を機能させる為の規制や仕組み
生産性を向上させ、高品質の製品を造るために必要な各種規制と仕組みの一例は次の通りです。
物理的規制
- タクトタイム規制
- 出来高表示規制
感情的規制
- 実績のグラフ化
- 競争意識を生む仕組み
- 生産性表彰制度
セル生産方式を導入する際には、これらのような規制や仕組みを運用しながら、作業者のモチベーションの維持向上を図っていかなければなりません。
規制と仕組みを上手く運用し、成果を生み出すための「セル」の構築を目指していきましょう!
いかがでしたか?セル生産方式の概要をイメージすることが出来たでしょうか?
セル生産のメリットと課題をしっかりと認識した上で、自社への導入の検討や自社流の生産方式づくりを目指していきましょう。
トヨタ生産方式について学ぶ!学習コースのご紹介
カイゼンベースの学習コースでは、トヨタ生産方式に関する具体的な内容を動画や理解度テストにより学習することが可能です。詳細の学習や実践でのご活用をご検討の方は、是非ご活用ください。
学習コース「k2-01:アニメで学ぶトヨタ生産方式~入門編~」
「トヨタ生産方式」は、製造業に勤める人はもちろん、社会人であれば知っておきたいテーマです。今でもなお進化し続けているトヨタ生産方式。生まれた背景から基本まで、その歴史や考え方を本講座では解説していきます。
学習コースの詳細
Lesson1:トヨタ生産方式って何?(5:21)
Lesson2:トヨタ生産方式の基本思想と2本柱(6:56)
Lesson3:トヨタ生産方式を創った3人の重要人物(7:13)
Lesson4:ジャストインタイムの3原則と後工程引き取り(5:41)
Lesson5:工程の流れ化とは?(7:44)
Lesson6:ボトルネック・ラインバランス・同期化(9:27)
Lesson7:必要数でタクトを決める(7:14)
Lesson8:ジャストインタイムと平準化(7:11)
Lesson9:ニンベンの付いた自働化の狙い(9:01)
Lesson10:ニンベンの付いた自働化の事例(7:29)
「Lesson1:トヨタ生産方式って何?」の動画はどなたでもご視聴頂けます。
「Lesson2:トヨタ生産方式の基本思想と2本柱」の動画は無料会員登録を行うことでご視聴が可能になります。
資料請求はこちらから
サービス紹介資料・価格表を無料でダウンロードできます。お気軽にお問い合わせください。
.png)
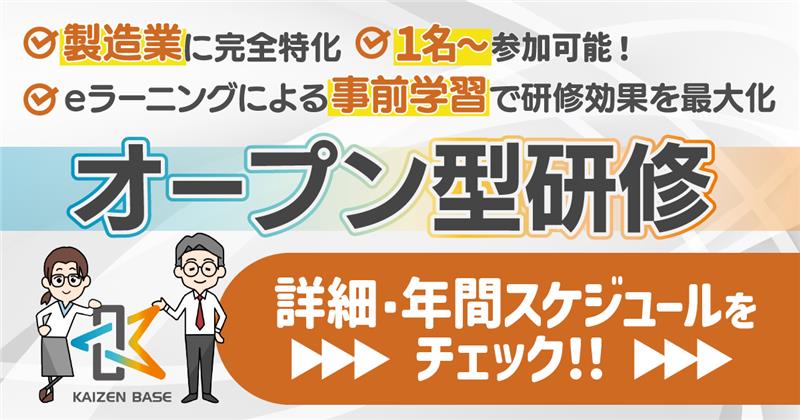
関連学習動画
-
k2-08
アニメで学ぶ“IE実践編~工程分析 Part1~”
有料サービス限定
Lesson3:単純工程分析とは
受講対象者
係長向け,次長・課長向け- カリキュラム構成
-
- 単純工程分析図
- 単純工程分析図(オペレーション・プロセス・チャート)
- 単純工程分析図の活用シーン
- 単純工程分析のステップ
- まとめ
-
k2-11
アニメで学ぶ“IE実践編~動作研究 Part2~”
有料サービス限定
Lesson6:サーブリッグ分析とは 後編
受講対象者
係長向け,次長・課長向け- カリキュラム構成
-
- サーブリック記号の3分類 Ⅱ類
- サーブリック記号の3分類 Ⅲ類
-
k2-12
アニメで学ぶ“IE実践編~時間研究 Part1~”
公開講座
Lesson1:時間研究の概要
受講対象者
係長向け,次長・課長向け- カリキュラム構成
-
- 時間研究の概要
- 時間研究の狙い
- 時間に関する3分類
- 時間研究の方法・視点
- まとめ
-
k2-18
アニメで学ぶIE実践編~応用手法 Part1~
無料会員限定
Lesson2:M-Mチャートの活用の仕方
受講対象者
全部門(管理職)- カリキュラム構成
-
- はじめに
- M-Mチャートの活用の仕方
- まとめ
-
k2-10
アニメで学ぶ“IE実践編~動作研究 Part1~”
公開講座
Lesson1:動作研究の狙い
受講対象者
係長向け,次長・課長向け- カリキュラム構成
-
- 動作研究の狙い
- モーション・マインドとは
- 体得すべきモーション・マインド
- まとめ
-
k2-23
アニメで学ぶトヨタ生産方式~中級編:自工程完結と継続的な品質改善~
無料会員限定
Lesson1:継続的品質改善に必要なこと(後編)
受講対象者
係長- カリキュラム構成
-
- はじめに
- 標準化の必要性
- 品質改善と維持管理の考え方
- まとめ