大部屋化による生産性向上の改善事例
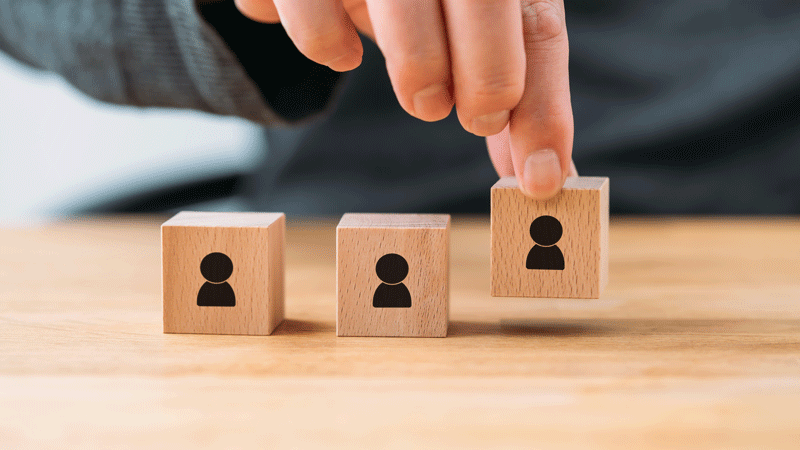
目次
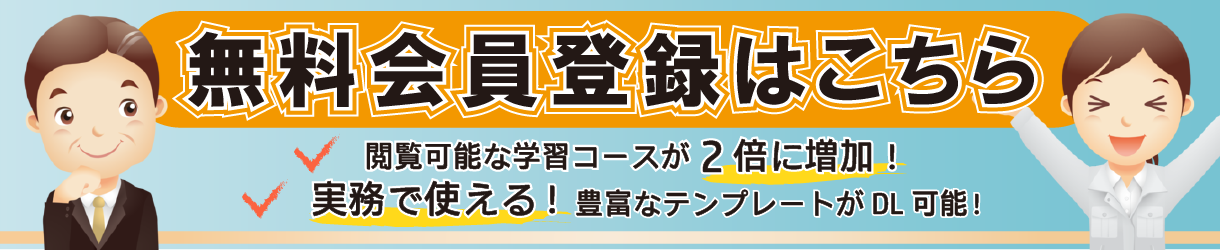
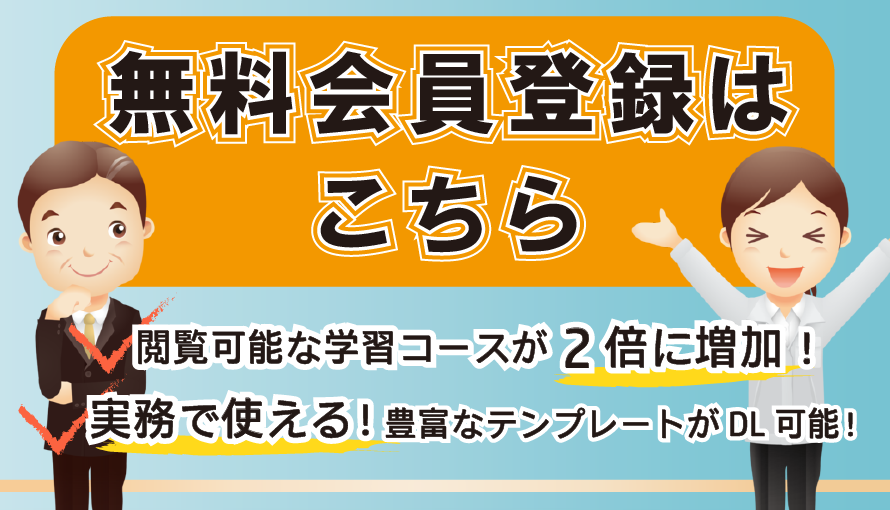
トヨタ生産方式の大部屋化の考え方を使ったカイゼン事例を紹介
日々の作業負荷の変動を「大部屋化」という考え方を導入し、人員配置の固定制からの脱却を図ったことで、生産性を大きく向上させた事例を紹介しています。
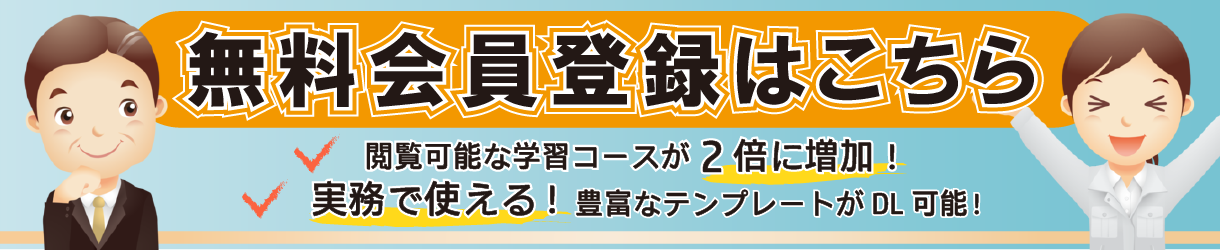
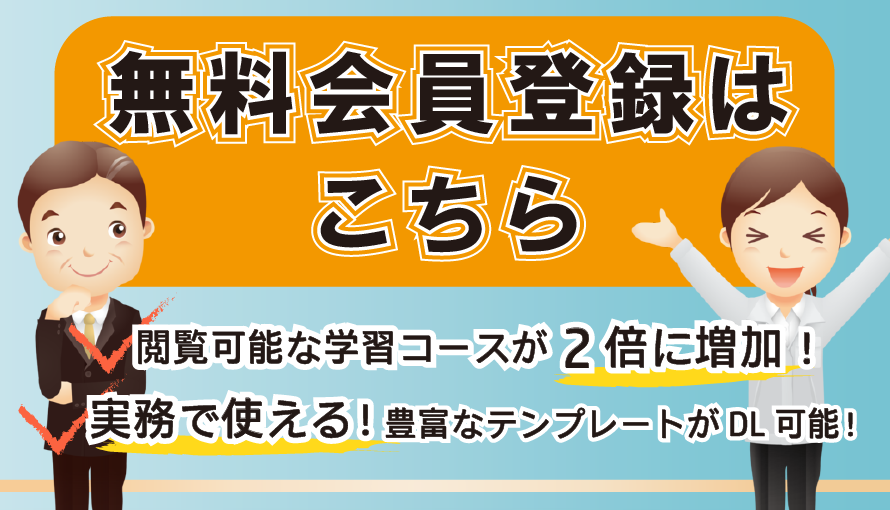
大部屋化による生産性向上の改善事例の紹介
現場における課題
まずは、現場における課題から確認します。
このグラフは、ある組立ラインの日々の作業負荷変動を表したものです。
この組立職場では、日々の生産負荷が激しく変動します。
そのためラインでは、その月の平均必要人数で人員を配置するものの、日別に見てみると、ある日は、配置された人員より作業量が少ないため手待ちや計画数以上の造りすぎが発生し、そしてまたある日は、作業量が設定より多く、後工程への供給遅延や残業が発生する等のことが生じています。
また、月平均の必要人員といっても、必ず割り切れる数字ではないため、例えば1.7人が必要人員である場合は、実際には2人の人員を配置して対応しています。
更に、残業でも対応しきれない程の高負荷日もあり、設定人員よりも多い人数を配置していることもあるため、複数のラインで同様な課題が発生しています。
大部屋化の導入前は・・・
ある日の設定工数
もう少し具体的なイメージで説明します。
例えば、ある3種類の組立工程があるとします。
日々の投入人員の推移は、このグラフのようになり、月平均の設定人員は、それぞれ1.5人、1.1人、1.4人となります。
従って、大部屋化を実施しない場合の実際の設定人員は、2人、1人、2人となります。
4人の設定人員に対して、5人を配置しているということになりますね。
一方、個別に日当たりの作業負荷を見てみると、例えば初日は、2.1人、0.7人、1.2人であり、組立2と組立3の工程では、手待ちや造りすぎが発生してしまう可能性があるのです。
翌日の設定工数
そして、2日目は組立3が忙しく、組立1,2に余裕があるというように、日によって負荷はバラバラになってしまいます。
このような状態が複数のラインで発生していたのでは、どうしても生産性が落ちてしまいますよね。
毎日同じ人員を配置すると・・・
以上のように、日々負荷変動の大きい職場では、毎日同じ人員を配置することは、手待ちのムダや造りすぎのムダを発生させてしまうことに繋がってしまいます。
そこで有効なのが、大部屋化です。
大部屋化の考え方を導入することで、人員固定制からの脱却が可能になります。
改善のアプローチ!
大部屋化とは
大部屋化とは、1人分の仕事量に満たない端数工数が存在する場合、複数のラインを1人または数人で受け持つことで、端数工数を吸収することを指します。
この考え方を使い、日々の作業負荷変動を複数ライン間で吸収しあうことで生産性の向上を目指すことにしました。
大部屋化の実際の運用イメージ
大部屋化の実施イメージを確認しましょう。
今回は、3つの組立工程を一つのグループとして考えます。
組立1は平均1.5人に対して1人、組立2は1.1人に対して1人、組立3は1.4人に対して1人というように、端数を除いて人員を設定します。
そして、リーダーを1人設け、全体のコントロールを行ないながら、遅延部分に応援に入ることにより、端数を吸収する役割も担います。
このように、組立1に応援が必要になった場合は、リーダーは組立1に入ります。
同様に、組立3に応援が必要になった場合は、組立3に応援に入ります。
このような考え方で大部屋化を運用することで、端数分を1人に集約することができ、従来5人で行なっていた方法と比べて、1人少ない人数での生産が可能となります。
大部屋化の効果
以上のように、いくつかの組立工程をグループ化し、端数を切り捨て少ない人員で投入することで、負荷変動を吸収する方式が大部屋化なのです。
大部屋化をうまく機能させるためには、多能工化とムダ取り、標準作業のつくり込み等が必要不可欠となります。
大部屋化実施、しかし・・・
さて、この職場の場合はどのような効果が出たのでしょうか。
実は、大部屋化を実施した当初は、いくつか問題があり、うまく機能しませんでした。
問題点としては、
・ルールがなく、応援するタイミングが定まらないこと
・そのため、応援タイミングの遅れが発生してしまうこと
・逆に、造り溜めしてしまう等のムダが発生してしまうこと
等が挙げられました。
大部屋化を機能させるための工夫
そこで、大部屋化を機能させるための工夫として、シューター化とゾーン分けを実施しました。
シューター化により、先入先出で何も考えずに手前からモノを動かすことができ、かつ残量が一目で分かるようになります。
また、赤ゾーン、黄ゾーン、緑ゾーンと色分けを行ない、応援タイミングの見える化を行なっています。
後工程に対する残量数を見える化
色分けのルールとしては、次の通りです。
赤ゾーンは、「欠品危険状態」とし、遅れ発生の危険があるため、リーダーが即座に応援を開始します。
黄ゾーンは、「注意状態」とし、このままでは遅れが発生するため、なるべく早めにリーダーは応援に入るようにします。
緑ゾーンは、「安全状態」とし、応援に入る必要が無いことを意味しています。
大部屋リーダーは、赤ゾーン、黄ゾーンで応援に入り、緑ゾーンになったら抜けるルールに統一することで、誰でもタイミングに迷わずに応援に入ったり抜けたりすることが出来るようになっています。
そして、ムダ取りも実施!
シューター化、ゾーン分けに加えて、ムダ取りも実施しています。
このグラフのように、製品群Xにおける機種別の能率の差を分析し、
能率が80%以下の足を引っ張っている機種にターゲットを絞り、ムダ取りと標準作業のつくり込みを実施することにしました。
1つ実際の作業改善内容を確認していきましょう。
部品配置のカイゼン Before
これはある組立工程の部品レイアウトと作業動線です。
本体を取り出し、小物部品、中物部品、大物部品を組付けていきます。
問題点としては、次のことが挙げられました。
- 中物部品の配置が左右逆となっており、右手、左手の取る位置が交差する部分がある。
- 大物部品を後ろから取り出さなければいけない配置になっており、振り向き作業が発生している。
- それらにより、複雑な作業動線になっている。
以上のように、部品配置の悪さが作業のムダを発生させており、1台の組付け時間(サイクルタイム)が、193秒掛かってしまっていました。
部品配置のカイゼン After
そこで、次のようなカイゼンを行ないました。
- 中物部品を手が交差なく作業できるように配置。
- 大物部品を前に配置し、振り向き作業を廃止。
- 部品配置の適正化により、作業動線が改善。
以上の改善の結果、サイクルタイムは193秒から7秒短縮し、186秒になりました。
さらに、楽に組付け作業が出来る様になり、作業負担も低減させることができています。
全体の改善結果!
それでは最後に、大部屋化によるライン全体の結果を確認してみましょう。
大部屋化前の能率は、約90%前後でした。
それが、大部屋化による改善を行なったことで、ライン全体の能率は47%も向上させることが出来ています。
人員配置の固定制から脱却することで、これ程までに大きな成果が出ることは大変参考になる良い事例ですね!
もちろん、大部屋化を実施するにあたっては、職場内コミュニケーション等の各種の課題が存在したはずです。
それらを1つずつ解決しながら進めてきたプロセスも、きっと職場にとって大きな財産になりますね!
この事例を参考に、あなたの職場でも改善を行ないましょう。
トヨタ生産方式について学ぶ!学習コースのご紹介
カイゼンベースの学習コースでは、トヨタ生産方式に関する具体的な内容を動画や理解度テストにより学習することが可能です。詳細の学習や実践でのご活用をご検討の方は、是非ご活用ください。
学習コース「k2-01:アニメで学ぶトヨタ生産方式~入門編~」
「トヨタ生産方式」は、製造業に勤める人はもちろん、社会人であれば知っておきたいテーマです。今でもなお進化し続けているトヨタ生産方式。生まれた背景から基本まで、その歴史や考え方を本講座では解説していきます。
学習コースの詳細
Lesson1:トヨタ生産方式って何?(5:21)
Lesson2:トヨタ生産方式の基本思想と2本柱(6:56)
Lesson3:トヨタ生産方式を創った3人の重要人物(7:13)
Lesson4:ジャストインタイムの3原則と後工程引き取り(5:41)
Lesson5:工程の流れ化とは?(7:44)
Lesson6:ボトルネック・ラインバランス・同期化(9:27)
Lesson7:必要数でタクトを決める(7:14)
Lesson8:ジャストインタイムと平準化(7:11)
Lesson9:ニンベンの付いた自働化の狙い(9:01)
Lesson10:ニンベンの付いた自働化の事例(7:29)
「Lesson1:トヨタ生産方式って何?」の動画はどなたでもご視聴頂けます。
「Lesson2:トヨタ生産方式の基本思想と2本柱」の動画は無料会員登録を行うことでご視聴が可能になります。
資料請求はこちらから
サービス紹介資料・価格表を無料でダウンロードできます。お気軽にお問い合わせください。
関連学習動画
-
k2-01
アニメで学ぶトヨタ生産方式~入門編~
有料サービス限定
6:ボトルネック・ラインバランス・同期化
受講対象者
現場部門, 間接部門, 一般, 主任・班長クラス, 係長クラス, 課長クラス- カリキュラム構成
-
- ボトルネック工程とは
- ラインバランス改善とは
- 同期化とは
- まとめ
-
k2-17
アニメで学ぶIE実践編~運搬分析 Part2~
公開講座
Lesson1:運搬活性分析
受講対象者
全部門(管理職)- カリキュラム構成
-
- はじめに
- 運搬活性分析とは
- 運搬活性示数の考え方
- 運搬活性分析図の作成方法
- まとめ
-
k2-11
アニメで学ぶ“IE実践編~動作研究 Part2~”
無料会員限定
Lesson2:両手作業分析とは
受講対象者
係長向け,次長・課長向け- カリキュラム構成
-
- 両手作業分析とは
- 両手作業分析の4区分
- まとめ
-
k2-04
アニメで学ぶ5S活動~5Sの概要と整理整頓編~
有料サービス限定
3:5Sによる効率の向上
受講対象者
現場部門, 間接部門, 新人, 一般, 主任・班長クラス, 係長クラス, 課長クラス- カリキュラム構成
-
- 5Sによる効率の向上とは
- 整理整頓ゲームで効果を確認
- モノ探しの年間ロスコスト
- まとめ
-
k2-14
アニメで学ぶIE実践編~稼働分析 Part1~
有料サービス限定
Lesson3:連続観測法
受講対象者
係長向け,次長・課長向け- カリキュラム構成
-
- 連続観測法とは
- 連続観測法の手順
- まとめ
-
k2-04
アニメで学ぶ5S活動~5Sの概要と整理整頓編~
公開講座
1:5S活動とは~5Sの定義と狙い~
受講対象者
現場部門, 間接部門, 新人, 一般, 主任・班長クラス, 係長クラス, 課長クラス- カリキュラム構成
-
- 5Sの定義とは
- 5S活動の目的
- 5Sが定着している職場の特徴?
- 5S活動において注意すべきこと
- まとめ