ロットとは?ロットの意味や製販で重要なロット管理の重要性を解説
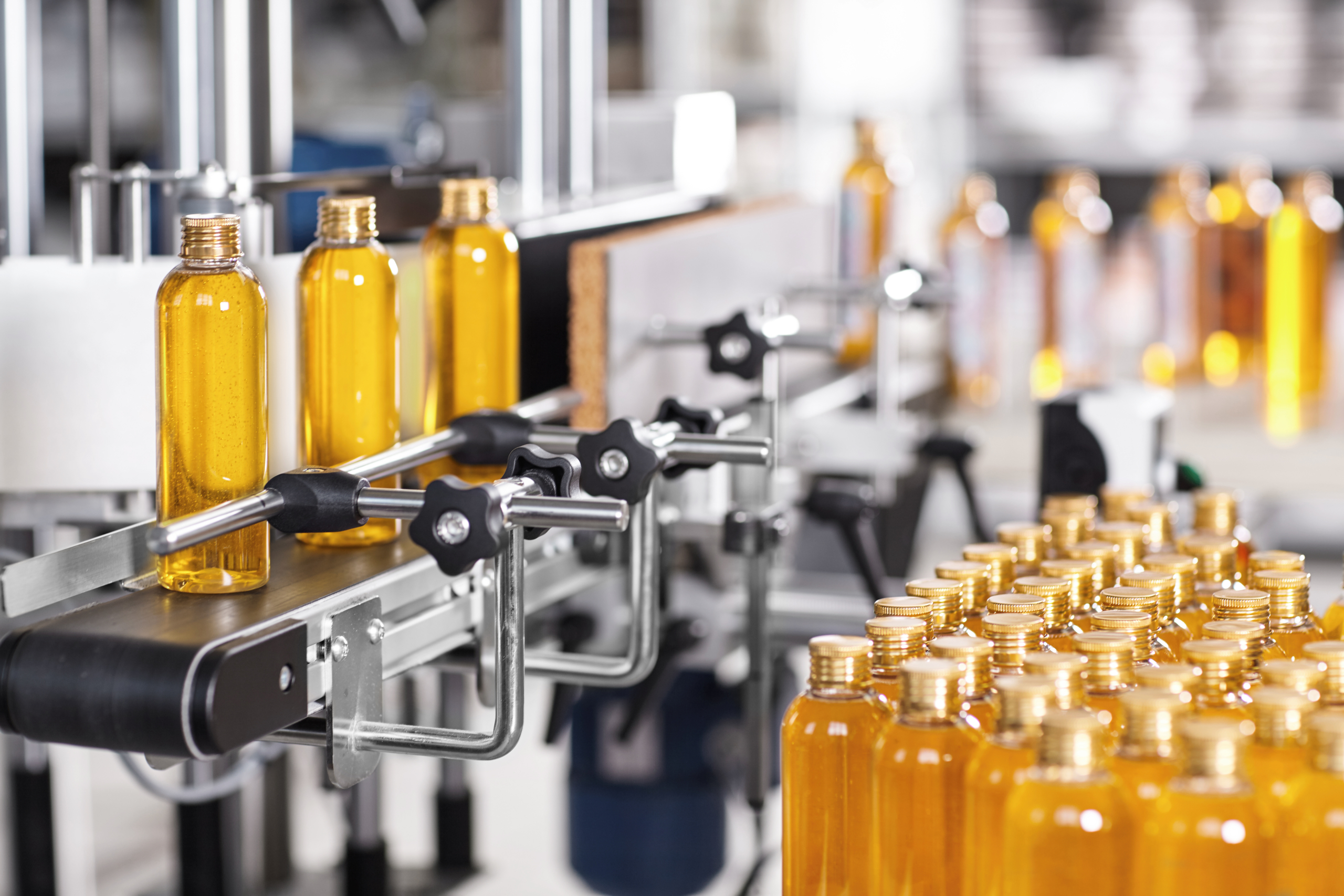
.png)
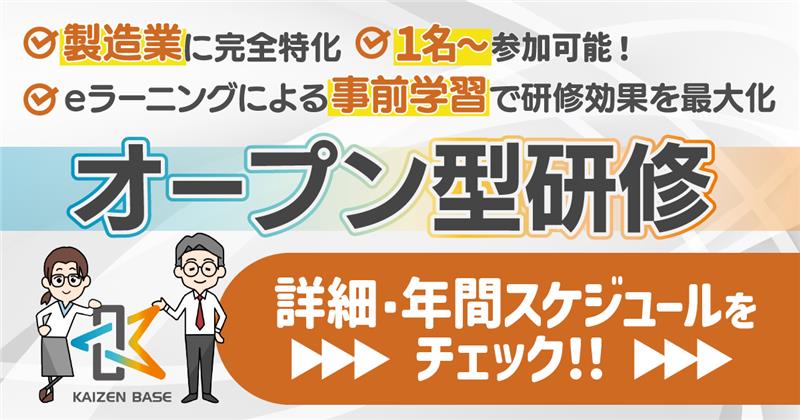
目次
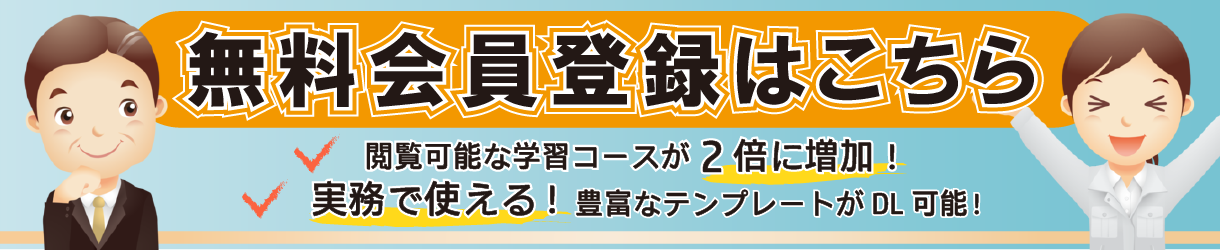
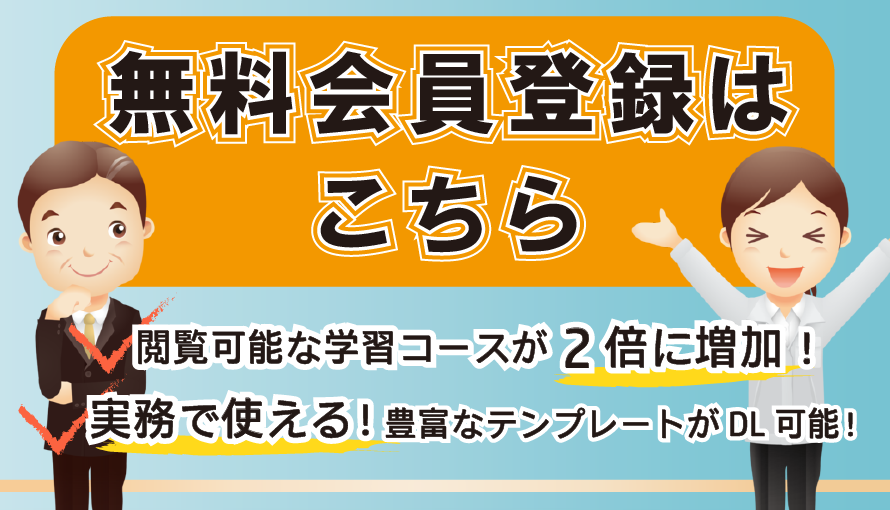
ロット(Lot)とは
ロット(Lot)の定義
ロット(Lot)とは、製品を製造する際の最小単位のことを指します。
複数の製品を製造している工場において、1つの製品を造る際に1回あたり「最低でもこの数(量)は連続して造る」という単位となります。
昨今、顧客ニーズの多様化により、同じものを大量に造るのではなく、様々な種類を製造し、「顧客に合ったものを、必要な時に、必要な分だけ提供する」という考え方がどの業界でも一般的になりました。しかし、製造現場では、完全に顧客にニーズに合わせて造ってしまうと、非効率な作業になってしまいます。なぜならば、製造工程では、違う種類の製品を造る時には、「切り替え作業(段取りと呼ばれます)」が発生するからです。
1日中同じ製品を造っていればたくさん造れるものの、違う種類の製品に変わってしまうと、段取りを行なう時間の分だけ造れる数(量)が減ってしまうのです。当然ながら、段取りを行なう回数分、この非効率性は大きくなります。
この段取りは、製品を造っている時間ではないため、言わば「価値を生まない時間」です。
人手不足が慢性化している現代では、造り手である工場から見ると、この価値を生まない段取りは極力少なくしたいと思うのは当然の気持ちでもあります。
とは言え、製造側の気持ちだけを優先してしまうと、顧客が離れていってしまいます。自社の都合を主張するばかりだと、「じゃあ結構です。他の会社にお願いしますね。」と言われてしまうのは目に見えているからです。
従って、顧客ニーズと製造の効率化の両方のバランスを取るために、ある一定の条件(=1回あたりの最低製造個数)を決める必要が出てくるのです。それが、「ロット」であり、生産管理においては欠かせない概念となります。
ロットという用語の使い方
例えば、1ロット(Lot)を100個と決めた場合には、注文は100個(1ロット)、200個(2ロット)、300個(3ロット)・・・・というような刻みで注文を受け付けるということになります。
顧客から注文を受ける場面では、
「この製品は最少ロットが200個ですので、200個単位で注文を受け付けます。」
といったような使い方をします。
製造ラインへ製造指示を出す場面では、
「A製品を5ロット、B製品を3ロット製造してください」
というような使い方をします。
製造ロット(Lot)の考え方
ロット(Lot)には、いくつかの種類があります。
1つは「受注ロット」です。注文ロット、購入ロットと呼ぶこともあります。これは、主に販売の現場で使います。もう1つは、「製造ロット」です。製造ロットとは、受注の個数と製造の個数を区別している場合に使用する用語です。
例えば、受注ロットは顧客ニーズを考慮し200個であるものの、製造を200個単位で行なうとあまりにも非効率である場合、製造ロットは1000個にするといったことを行ないます。この場合、注文以上に造っているので在庫が発生するため、その後にも同じ製品の注文があると予想され、「売れ残りが発生しない」ことが前提となります。
なお、実務においては、基本的には「顧客ニーズに合わせたロットの設定」が求められますが、状況によっては交渉の余地がある場合もあります。例えば、製造側では、「価格を引き下げる代わりにロットを少し大きめに設定させてもらう」といった交渉はよくあることです。一方、購入側では、最少ロットよりも少ない数を注文させてもらう代わりに、価格アップを了承するという交渉もあります。
これらの交渉は、必ずしも受け入れられるとは限りません。ただし、このような交渉を行なうことは決して悪いことではありません。一方的に要求するのはよろしくありませんが、双方が合意するのであれば、むしろ積極的に行うべきものでもあるのです。
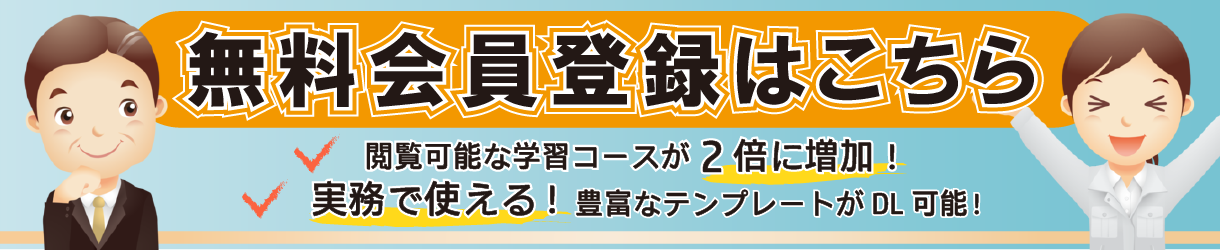
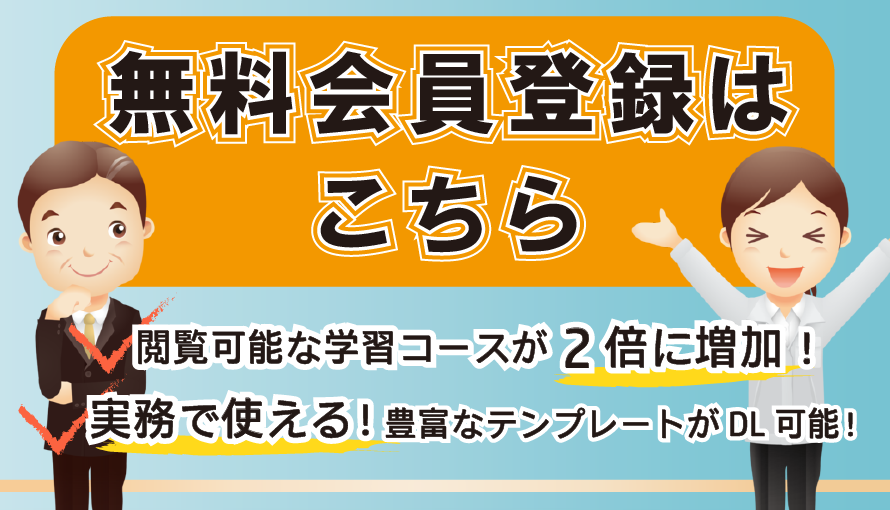
ロット(Lot)管理の重要性
品質保証において大切なロット管理
ロットには、もう1つ大事な側面があります。「ロット管理」という考え方です。
品質保証においては、不具合が発生した時には、後から遡って原因究明を行なうことが必要不可欠です。その際、どの材料で製造したのか、どんな条件で製造したのか等をロットという単位で管理を行ないます。
一般に、不良が1個発生した時には、その前後に造ったものも不良である可能性が出てきます。もし顧客に納品した後に不良品が見つかったとすると、不良品の可能性があるものは回収しなければなりません。その際に、「どこまでを調査するか」「どこまでを回収するか」といった問題が起きます。
ロット管理をしっかりと行っていれば、対象ロットをすぐに特定できます。それにより、スムーズに対応を行なうこともでき、対応コストも最小限に抑えることが可能となるのです。一方、しっかりとロット管理できていない場合、例えばリコール発生時には、莫大な損失が出ることや、対象範囲が不十分であると、「リコールよりも自分たちを優先した」と言われてしまい、社会的な信頼も失墜しかねません。つまり、ロット生産を行なっている会社では、ロット管理は「出来ていて当たり前」のものであると認識すべきとも言えます。
ロット(Lot)管理における注意事項
ここまでで説明したように、ロットは製品の製造や販売はもちろん、管理を効率的に行なうための仕組みでもあります。そして、ロット管理における1番の注意事項は、「製造側の都合を優先し過ぎないこと」です。「たくさんまとめて造った方が効率的だ」というのは、もちろんその通りですが、顧客の感覚から離れてしまうと、一気に見放されてしまうリスクを認識しなければなりません。
従って、「もっと小さいロットで造ることが出来ないのか」という視点を製造側は常に持ち続けることが必要不可欠なのです。
現代では、消費者ニーズは多様化しており、今後も益々それは進んでいくと予想されます。そういった時代では、消費者のニーズに合わせた生産活動を行なうことができない企業は、よほど差別化された魅力的な製品を持たない限り、淘汰される運命にあります。
競合他社は今日も「小ロット化」のために改善を行なっているかもしれません。自分たちが想像している以上に、顧客対応力が上がっているかもしれません。
この危機感を持つことが競争に勝ち残っていくための出発点となるのです。
小ロット化のために行なう「段取り改善」
では、どのようなことを行なって小ロット化を進めていけばよいのでしょうか。
代表的な取り組みは、「段取り改善」です。
製品の種類が変わる時、「段取りが発生するために効率が落ちる」ことは既に説明しましたが、これは逆に言うと、「段取り時間さえ短くすることが出来れば、製品の種類が多くても効率の低下を最小限にできる」ということでもあります。
段取り時間とは、「前の種類の製品の製造が終わった瞬間から次の種類の製品の1個目の良品が出来るまで」の時間のことを指します。例えば、製造現場における段取り作業では、
・部品、治具等の準備や交換
・片付け、清掃
・製造条件の設定
等が挙げられます。これらの作業が短い時間で出来ればよいのです。
いかに最短で行なうことができるかについては、作業分析等を行ないながら、改善を繰り返していきます。具体的な段取り改善の方法は、別コラムにて解説しますが、まずは本ページでは、小ロット化の流れは今後も継続すること、そのために段取り改善が必要不可欠であることを覚えておきましょう。
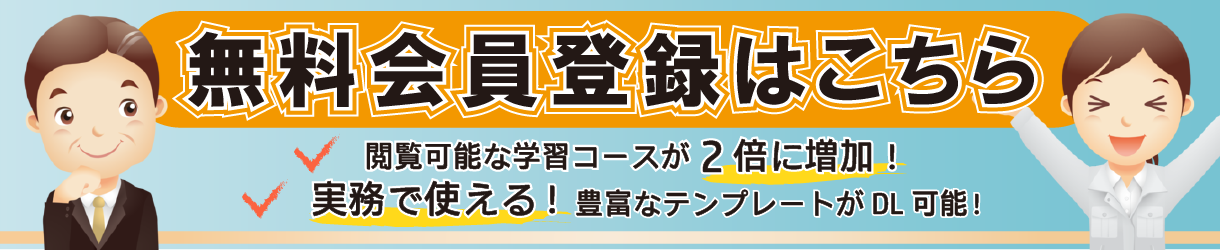
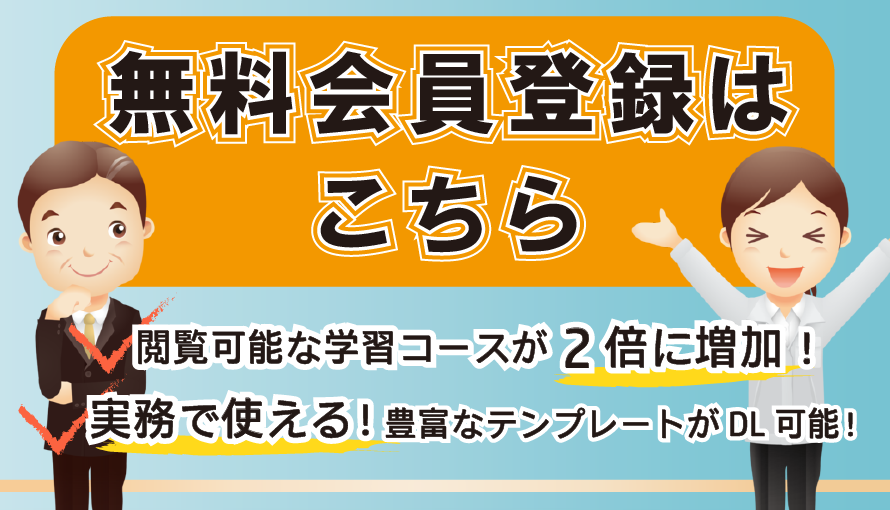
ロット、ロット管理まとめ
ロットの扱い方は、会社としてしっかりと明確にしておかなければなりません。
実務においては、製造側の「ロットは大きければ大きいほどよい」という意見と、販売側の「ロットは小さければ小さいほどよい」という意見がぶつかり合い、両極端の議論になってしまうことがあります。しかし、このようなイチかゼロかの議論では前に進むことができません。
大切なことは、将来目指したい姿(どのくらい細かい顧客ニーズまで対応するか)を明確化し共有した上で、現状の実力をしっかりと見極め、実力ベースで製販のバランスを取りながら協力していくことだと頭に入れておきましょう。
いかがでしたでしょうか?
ロット(Lot)に関する基本的な考え方はイメージできましたか?簡単そうで実は奥が深いロットの考え方。しっかりと意味を理解した上で日々の実務を行なっていると、今まで見えなかった課題が見つかるかもしれません。
在庫管理について学ぶ!学習コースのご紹介
カイゼンベースの学習コースでは、在庫管理に関する具体的な内容を動画や理解度テストにより学習することが可能です。詳細の学習や実践でのご活用をご検討の方は、是非ご活用ください。
学習コースの概要「k3-51:在庫管理と在庫削減の進め方」
在庫管理の基本を学び、実務で在庫削減を実践できるレベルを目指すコースです。在庫管理の全体像、専門用語、在庫削減の考え方や進め方を身に付け、職場の困りごとを解決するために、日常活動やプロジェクト活動に取り組んでいきましょう!
学習コースの詳細
Lesson1a:在庫管理の重要性(前編)(8:07)
Lesson1b:在庫管理の重要性(後編)(12:08)
Lesson2a:在庫管理の進め方(前編)(11:21)
Lesson2b:在庫管理の進め方(後編)(10:25)
Lesson3a:発注方式と安全在庫(前編)(12:04)
Lesson3b:発注方式と安全在庫(後編)(11:47)
Lesson4:ロケーション管理と在庫最適化(17:26)
「Lesson1:在庫管理の重要性(前編)」の動画はどなたでもご視聴頂けます。
「Lesson2:在庫管理の重要性(後編)」の動画は無料会員登録を行うことでご視聴が可能になります。
資料請求はこちらから
サービス紹介資料・価格表を無料でダウンロードできます。お気軽にお問い合わせください。
.png)
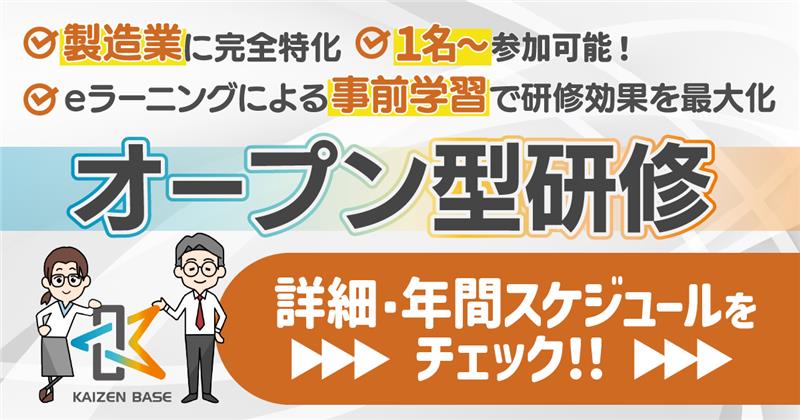
関連学習動画
-
k2-28
アニメで学ぶトヨタ生産方式~中級編:標準作業~
無料会員限定
Lesson2:標準作業:繰り返し作業(前編)
受講対象者
主任・班長- カリキュラム構成
-
- はじめに
- 標準作業のタイプ
- 工程別能力表の作り方
- 標準作業組合せ票の作り方
-
k2-05
アニメで学ぶ5S活動~清掃・清潔・躾編~
有料サービス限定
4:清潔のポイント① 予防整理・予防整頓・予防清掃
受講対象者
現場部門, 間接部門, 主任・班長クラス, 係長クラス, 課長クラス- カリキュラム構成
-
- 予防整理、予防整頓、予防清掃とは
- 清潔「事後から予防へ」
- なぜなぜ分析と対策
- まとめ
-
k2-27
アニメで学ぶ管理・監督者による安全職場の仕組みづくり
公開講座
Lesson3以降は、有料会員サービスで限定公開中!
受講対象者
次長・課長- カリキュラム構成
-
アニメで学ぶ管理・監督者による安全職場の仕組みづくり
Lesson1:企業にとっての『安全』を知る
Lesson2:職場の現実から『危険』を知る
Lesson3:活動を継続させる『仕組み』を作る ※有料会員向け限定
Lesson4:仕組みも人も『進化』を睨み育てる ※有料会員向け限定
-
k2-01
アニメで学ぶトヨタ生産方式~入門編~
無料会員限定
2:トヨタ生産方式の基本思想と2本柱
受講対象者
現場部門, 間接部門, 一般, 主任・班長クラス, 係長クラス, 課長クラス- カリキュラム構成
-
- トヨタ生産方式の基本思想とは
- トヨタ生産方式の2本柱とは
- ジャストインタイムとは
- ニンベンの付いた自働化とは
- まとめ
-
k2-11
アニメで学ぶ“IE実践編~動作研究 Part2~”
有料サービス限定
Lesson5:サーブリッグ分析とは 前編
受講対象者
係長向け,次長・課長向け- カリキュラム構成
-
- サーブリック分析とは
- サーブリック分析の狙い
- サーブリック記号の3分類 Ⅰ類
-
k2-01
アニメで学ぶトヨタ生産方式~入門編~
有料サービス限定
6:ボトルネック・ラインバランス・同期化
受講対象者
現場部門, 間接部門, 一般, 主任・班長クラス, 係長クラス, 課長クラス- カリキュラム構成
-
- ボトルネック工程とは
- ラインバランス改善とは
- 同期化とは
- まとめ