ラインバランス分析とは?効率よくスムーズな生産の流れを実現するためのIE手法を解説
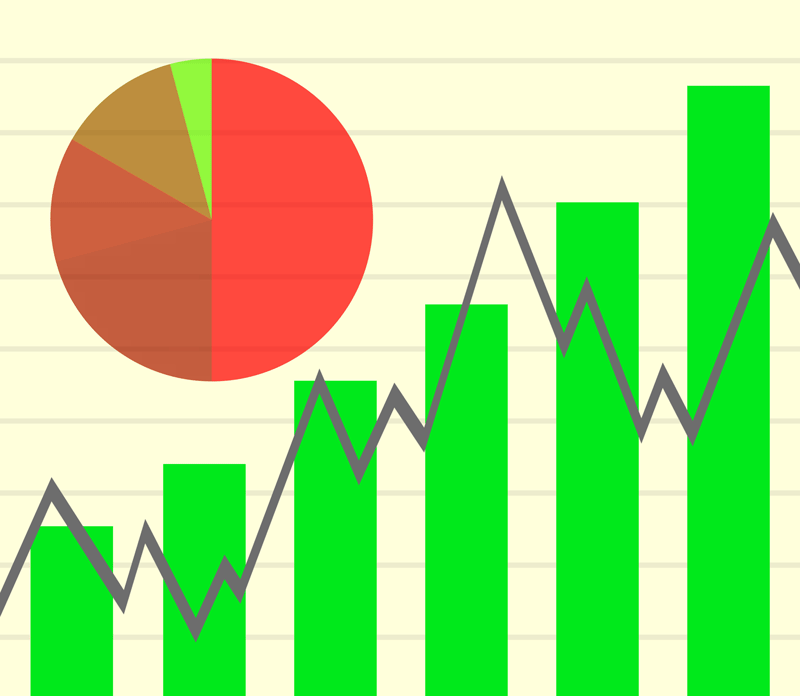
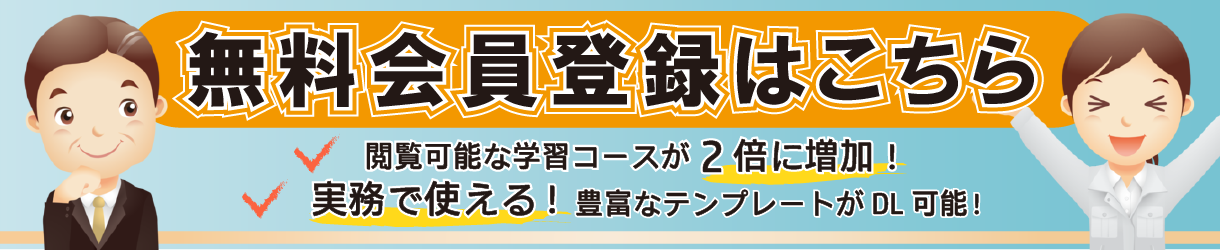
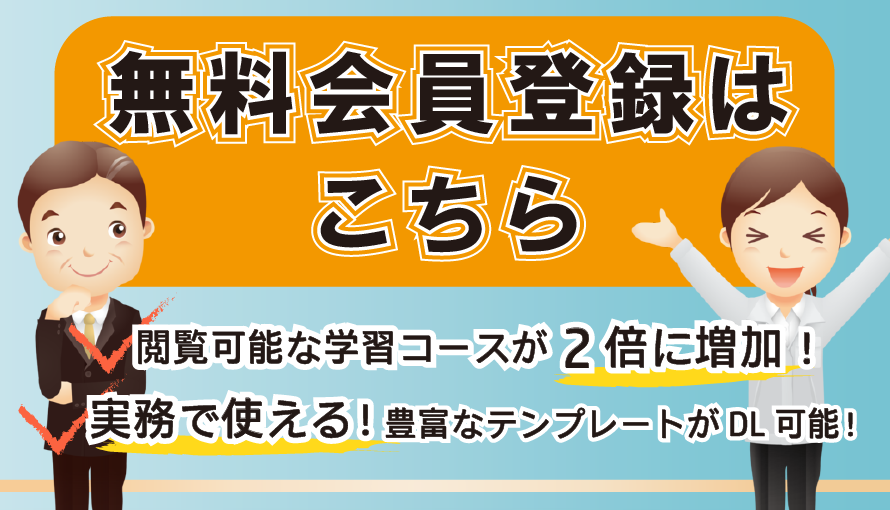
ラインバランス分析とは
ラインバランス分析は工程分析と時間研究の応用的な手法
ラインバランス分析とは、生産ラインにおける各工程の能力の差をなくし、効率の良いスムーズな生産の流れを実現するための分析のことです。
本ページでは、工程間のラインバランスを適正化し、効率よくスムーズな生産の流れを実現するために欠かせない、ラインバランス分析について解説をしていきます。
ラインバランス分析は、工程分析と時間研究の応用的な手法となります。
ラインバランス分析の活用場面は次の通りです。
・人の能率を向上させたい時
・機械の稼働率を向上させたい時
・リードタイムを短縮させたい時
・機械化、省力化を行いたい時
・工程設計や工程編成を検討する時
このように、様々な場面でラインバランス分析は活用されています。IEに関してはよく知らなくても、ラインバランスという言葉は聞いたことがあるという人も多いかもしれません。
分業について
一般に、生産効率を向上させるためには、製造プロセスをいくつかの工程に分け、分業することが不可欠です。1つの工程で全ての作業が完了する方が珍しいと言えます。分業はどんな会社でも行っているごくごく当然のことなのです。
ここでワンポイントです。分業という言葉の定義を明確にしましょう。各工程・各作業を作業者で分担し、同じ作業を繰り返すことを分業と言います。分業することで、作業が簡素化・専門化され、生産効率の向上に有効な手段とされています。
さて、分業による効率化と言葉で言うのは簡単ですが、実際にはそんなに簡単ではありません。例えば、各工程における作業時間のバラツキ、設備能力差による稼働時間のバラツキ等はよく発生する問題です。これらのバラツキにより、作業者の手待ちの発生、仕掛品の発生などに繋がってしまうのです。
IEの実践においては非常に大切なラインバランス
例えば、3つの工程があり、作業時間がそれぞれ、7分、10分、3分とバランスが取れていない場合、どのような問題が発生するでしょうか。
そう、工程1と工程2の間には、仕掛滞留が発生し、ムダな運搬、ムダなスペースの発生に繋がってしまいます。また、工程2と工程3の間には手待ちが発生し、効率の低下に繋がってしまうのです。
完全なラインバランスを取ることは不可能であるものの、極力その目標に近づけることが、IEの実践においては非常に大切な視点となります。
工程間・工程内のモノの流れが生産効率を左右している
工場内には、様々な工程があり、工程間・工程内のモノの流れが生産効率を左右していると言っても過言ではありません。工程間のラインバランスが整っていることで、淀みの無い流れるような生産が可能となるのです。
ラインバランス分析を行うことで、ボトルネック工程の明確化、必要バッファの明確化、ラインバランス効率・編成効率の改善などを進めていくことができます。
その結果、リードタイム短縮、生産性向上、仕掛在庫削減といったメリットに繋がっていくのです。
生産性向上の基本“ボトルネック”改善
それでは次に、生産性向上の基本である、ボトルネック改善について確認していきましょう。
各工程の生産能力のバランスが生産性に大きく影響
生産工程が複数の工程で構成されている場合、生産ラインを構成する各工程の生産能力のバランスが生産性に大きく影響します。そのため、時間当たりの処理量等の生産能力は各工程でどのくらいなのか、その差はどのくらいあるのかを数値で明確にすることが欠かせないのです。
製品毎、機種群毎等に各工程の生産能力を見える化し、ボトルネック工程を特定、改善を行うという流れは、生産工程の改善の基本です。今一番ボトルネックになっている工程はどこなのか、それをどうやって改善するのかを常に考え続けていきましょう。
では、ボトルネック改善はなぜ大切なのか、もう少し詳細を確認していきましょう。
考えてみれば当然
例えば、どれだけ第1工程が早く造っても、第2工程がその分を造れなければ、ただ仕掛在庫が溜まってしまうだけです。考えてみれば当然ですが、この当たり前が抜けていることが意外と多いものです。
前の工程あるいは後ろの工程の能力以上に作業を進めても、結局は仕掛在庫の増加や手待ちの発生に繋がってしまうだけですよね。
どこかが頑張っても沢山出荷ができるわけではない
つまり、生産ラインは、リレーとは違い、どこかが頑張っても沢山出荷ができるわけではないのです。
このように、5つの工程を人に例えて考えてみましょう。第1工程は能力10、第2工程は能力12、第3工程は能力5、第4工程は能力8、第5工程は能力15、というように人の能力にバラツキがあると仮定します。
この状況では、第3工程の能力が一番低いということになります。この一番能力が低い人、低い工程が、「ボトルネック工程」と呼ばれます。
生産工程においては、ボトルネック工程である第3工程の能力に合わせて、他の工程も能力5で造るのが一番ムダがありません。ボトルネック工程以外が、ボトルネック工程以上の能力で作業を行なうと、仕掛在庫の増加による運搬効率の悪化等により、効率は上がるどころか、むしろ下がってしまいます。
従って、まずはボトルネック工程に合わせた生産を行なうことが一番ムダがないということを覚えておきましょう。
ボトルネック工程の能力アップが必要不可欠
そして、ラインの生産性を向上させるには、ボトルネック工程の能力アップが必要不可欠となります。この場合、第3工程の作業に対して、もっと早く造る・もっと沢山造るにはどうしたらよいかを考えて改善します。
どの工程がボトルネックになっているか?
改善の結果、第3工程の能力が10まで上がったとします。すると、今度はボトルネック工程が第4工程に移ります。
つまり、ボトルネックは必ず特定の工程というわけではなく、改善によって移り変わるものであるため、「現在はどの工程がボトルネックになっているか」を日々把握しておかなければいけません。
この場合、第4工程にボトルネックが移り変わったため、今度は第4工程の能力を上げるための改善を考えて実行していきます。
これがラインバランス改善
このようにボトルネック工程対策を繰り返すと、全体の能力が向上し、生産性が上がっていくのです。今回の場合、初めは全工程が能力5に合わせて作業していたのに対して、ボトルネック工程対策を行なったことにより、能力10で作業を行なえるようになりました。
生産性を上げるための一番大事な手段は、ボトルネック工程の対策をすることであるとしっかりと覚えておきましょう。ボトルネック工程を改善し、全体のバランスを取ることを「ラインバランス改善」と呼びます。
なお、製品によってボトルネック工程が変化する場合があります。先入観や1つの製品の状況だけで判断せずに、しっかりと現状分析をした上で改善を進めるようにしましょう。
ライン内作業でも同じ
以上のことは、ライン内の作業においても同じように考えます。
少し極端な例ですが、1つのライン上で12名が流れ作業を行なっている状況を対象とすると、もし、左から4,6,8番目の作業者が1分間に造れる個数が、他の作業者と比べて半分の50個である時、どのようなラインの能力設定を行うでしょうか。
恐らくこの場合、何も考えずに能力設定を行なうと、一番能力が低いボトルネック工程に合わせて、1分間に50個の能力設定をすることになります。しかし、他の作業者には余裕があるので、この設定ではムダが大きいですよね。
一番遅い工程を早くすることで全体を早くする
そこで、ボトルネック工程の作業を前後の作業者に分担し直すことでボトルネックの改善を行ないます。作業の分担の見直しにより、50であった能力が90まで上がると、ライン全体の能力設定も50から90まで上げることが出来るようになります。
これがボトルネック対策の基本的な考え方です。一番遅い工程を早くすることで全体を早くする、これが大きな生産性向上に繋がることになるのです。
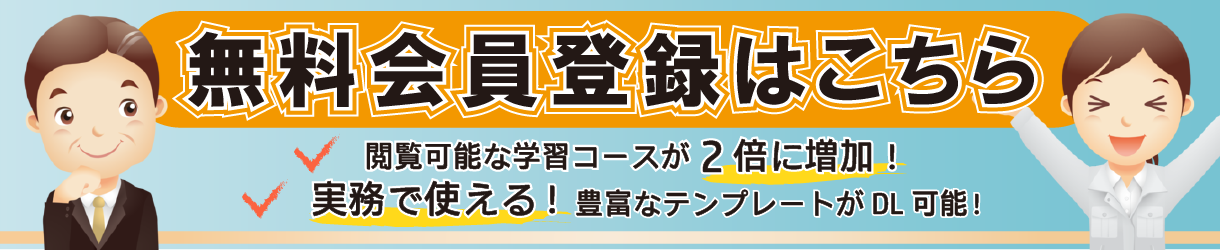
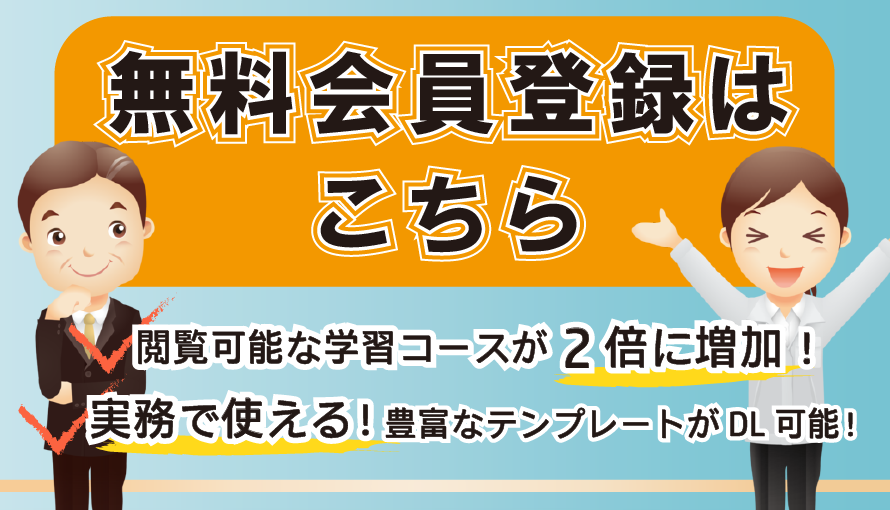
ラインバランス分析の進め方
それでは次に、ラインバランス分析の進め方について確認します。
ラインバランス改善のステップ
ラインバランス改善のステップは次の通りです。
まずは対象選定です。作業量(生産量)が多いものから順番に行なうようにしましょう。
次に作業時間分析を行ないます。5ゲン主義を忘れずに、動画を活用する等により進めていきます。
次にラインバランスの見える化です。数値・グラフで見える化することが大切です。
そして改善を実施する、というステップを繰り返していきます。
ラインバランスを見える化する
ラインバランスを見える化する際には、ここに示すような見える化シートを活用していきましょう。
サイクルタイムに対する、ロス時間、ムダの発生割合、正味作業時間の割合、各種分析値、要素作業一覧を書き込んでいくことで、どの工程にどのくらいバランスロスが発生しているかを可視化することができます。
感覚論ではなくしっかりと数字で把握することで、今までに気付き難かったムダを発見することができ、改善も進んでいくのです。
目標ラインは90%以上
なお、ラインバランス効率は、「各工程の作業時間の合計×100」を「最長工程の作業時間×人員数」で割ったもので求められます。
目標ラインは90%以上、必達ラインは80%を基準に改善を行なうようにしましょう。対象となる工程の種類によって、目指すべき水準は変わるため、数字はあくまで目安として捉えてください。
ラインバランス改善の基本パターン
それでは次に、ラインバランス改善の基本パターンについて確認しましょう。
ラインバランス改善の基本4パターン
ラインバランス改善を行なう上での基本パターンは次の4つです。
パターン1は、ネック工程の作業の一部を他の工程に分配する方法です。時間が掛かっている工程の負担を下げることで、全体のサイクルタイムを短縮します。
パターン2は、作業改善や工程の機械化により、ネック工程の作業時間を短縮する方法です。設備の能力アップにより作業時間を短縮したり、経験のある特殊技能の高い熟練者を配置し、作業時間を短縮させたりします。
パターン3は、作業を分割し、他工程に分配してその工程をなくす方法です。サイクルタイムは変えずに、人員を減らすことで効率アップを狙います。
パターン4は、ネック工程を分割し、工程数(作業者数)を増やす方法です。人員を増やしますが、全体のサイクルタイムを大きく短縮することで効率アップを狙います。
基本はこの4パターンですが、各パターンの組合せ等、無数の方法があります。改善するラインに応じて柔軟に考えるようにしてください。
ラインバランス改善事例(パターン3)
では、パターン3でラインバランス改善を行った事例を確認してみましょう。ここに示しているグラフは、ラインバランスシートを使用し、手待ち・余裕を見える化したものです。
各作業に対する作業時間を測定し、レーティングを考慮して数値化しています。
数値化した結果、前後工程の能力バランスを考えると、スピードを少し落としても問題ないことが分かりました。そこで、人員を減らし各作業者の負荷を平準化するという改善を行うことにしました。
結果、余裕があった作業者の負荷が適正化されたことでレーティングも向上し、ラインバランス効率も64%から84%に改善しています。9人作業を7人作業に省人化できたことも大きな効果ですね。
現代に合わせた勝ちパターンをつくろう
なお、近年、従来から行われてきた“分析型”のラインバランス改善が実務にそぐわなくなってきています。多品種少量、商品の短命化等により、時間を掛けて分析してもすぐに製品が入れ替わってしまうからです。
従って、現代に合わせた勝ちパターンをつくっていかなければいけません。生産量が多い商品でじっくり分析して結果を出し、横展開を進めて、商品開発から現場生産までに作業をつくり込む体制へと変えていくのです。
製品の入れ替わりが多くてもしっかりと儲けられる体質を目指していきましょう。
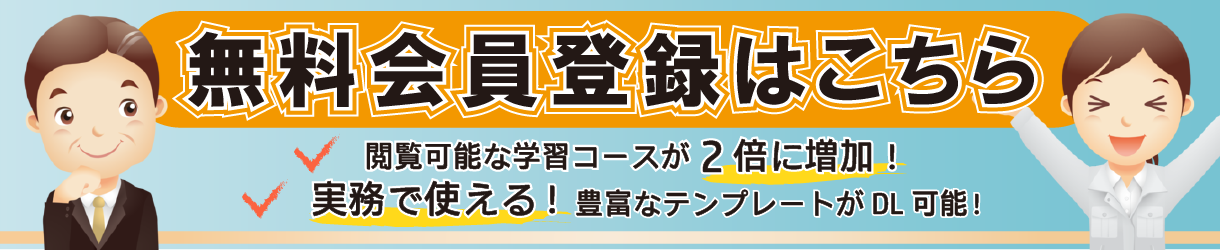
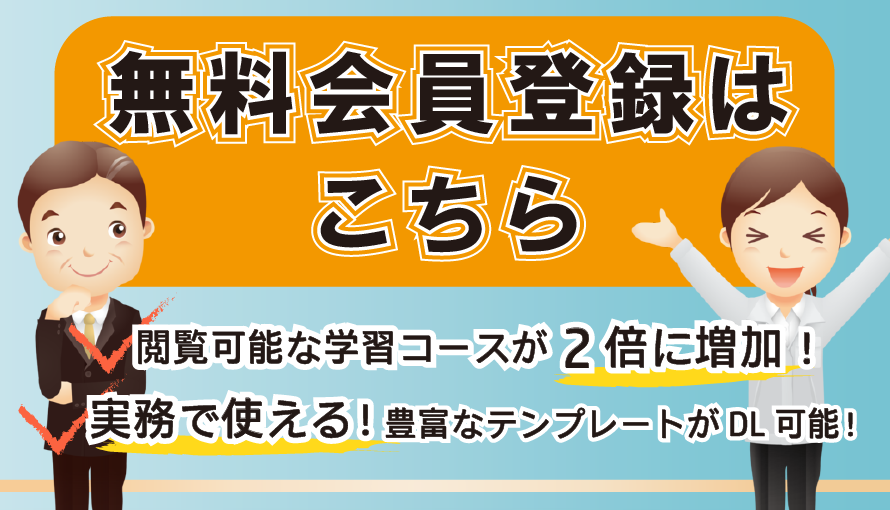
ラインバランス分析のまとめ
以上で学んだことをまとめてみましょう。
ラインバランス分析とは?
- ラインバランス分析とは、生産ラインにおける各工程の能力の差をなくし、効率の良いスムーズな生産の流れを実現するための分析のこと
- ラインバランス分析は、人の能率を向上させたい時、機械の稼働率を向上させたい時、リードタイムを短縮させたい時、機械化、省力化を行いたい時、工程設計や工程編成を検討する時等に活用される
- ラインバランス効率とは「各工程の作業時間の合計×100」を「最長工程の作業時間×人員数」で割ったもの。目標ラインは90%以上、必達ラインは80%を基準に改善を行なう
いかがでしたか?連合作業分析の概要はイメージできましたか?
生産現場だけではなく、事務所、工事現場、病院、交通機関等、様々な場面で発生する組み合わせ作業。M-MチャートやManチャートを使ってより効率的な組み合わせで作業が行えるようにしていきたいですね!
参考文献
・新版IEの基礎(著:藤田彰久 、建帛社、1997年)
・現場実践シリーズ IE7つ道具(著:杉原寛 他 、日刊工業新聞社、1993年)
IE実践の応用的手法について学ぶ!学習コースのご紹介
カイゼンベースの学習コースでは、IE実践の応用的手法に関する具体的な内容を動画や理解度テストにより学習することが可能です。詳細の学習や実践でのご活用をご検討の方は、是非ご活用ください。
学習コース「k2-18:アニメで学ぶIE実践編~応用手法 Part1~」
本講座では、これまでに学んだIEの基本となる手法を組み合わせた応用手法について学ぶことができます。2種類の連合作業分析表の活用方法など、本講座にて詳しく学習しましょう。
学習コースの詳細
Lesson1:連合作業分析とは(4:53)
Lesson2:M-Mチャートの活用の仕方(4:28)
Lesson3:M-Mチャートの事例(5:02)
Lesson4:Manチャートの活用の仕方(4:29)
Lesson5:Manチャートの事例(5:15)
「Lesson1:連合作業分析とは」の動画はどなたでもご視聴頂けます。
「Lesson2:M-Mチャートの活用の仕方」の動画は無料会員登録を行うことでご視聴が可能になります。
学習コース「k2-19:アニメで学ぶIE実践編~応用手法 Part2~」
本講座では、「ラインバランス分析」をはじめ「レイアウト改善の6つの視点」についてなど、各IE分析を組み合わせた応用手法について学習することができます。成果を出すためのIE改善を本講座で学び、実践に活かしていきましょう!
学習コースの詳細
Lesson1:ラインバランス分析とは(6:59)
Lesson2:ラインバランス分析の進め方と基本パターン(5:38)
Lesson3:プラント・レイアウトの基本(6:05)
Lesson4:レイアウトの検討方法(7:00)
Lesson5:レイアウト改善の6つの視点 前編(6:03)
Lesson6:レイアウト改善の6つの視点 後編(6:09)
「Lesson1:ラインバランス分析とは」の動画はどなたでもご視聴頂けます。
「Lesson2:ラインバランス分析の進め方と基本パターン」の動画は無料会員登録を行うことでご視聴が可能になります。
資料請求はこちらから
サービス紹介資料・価格表を無料でダウンロードできます。お気軽にお問い合わせください。
関連学習動画
-
k2-06
アニメで学ぶ“IE入門~IE手法の概要編~”
有料サービス限定
6:組み合わせ手法の概要
受講対象者
現場部門, 間接部門, 主任・班長クラス, 係長クラス, 課長クラス- カリキュラム構成
-
- ①連合作業分析
- ②ラインバランス分析
- ③プラント・レイアウトト
- 各分析手法の位置づけを生産の流れ
- まとめ
-
k2-06
アニメで学ぶ“IE入門~IE手法の概要編~”
公開講座
1:IE・インダストリアルエンジニアリングとは
受講対象者
現場部門, 間接部門, 主任・班長クラス, 係長クラス, 課長クラス- カリキュラム構成
-
- IEとは
- IE手法活用の1番の狙い
- IEのメリット
- まとめ
-
k2-06
アニメで学ぶ“IE入門~IE手法の概要編~”
有料サービス限定
3:IEにおける各種手法
受講対象者
現場部門, 間接部門, 主任・班長クラス, 係長クラス, 課長クラス- カリキュラム構成
-
- IEにおける各種手法
- IE(≒作業研究)は大きく2つに分類される
- 方法研究と作業測定を組み合わせた応用的な手法
- 各種手法の活用シーン
- まとめ
-
k2-06
アニメで学ぶ“IE入門~IE手法の概要編~”
無料会員限定
2:テーラーとギルブレスの功績
受講対象者
現場部門, 間接部門, 主任・班長クラス, 係長クラス, 課長クラス- カリキュラム構成
-
- IEの父と呼ばれる2人の人物
- テーラー|シャベルすくいの実験を行った人物
- ギルブレス|レンガ積みの研究を行った人物
-
k2-06
アニメで学ぶ“IE入門~IE手法の概要編~”
有料サービス限定
4:方法研究に関する手法の概要
受講対象者
現場部門, 間接部門, 主任・班長クラス, 係長クラス, 課長クラス- カリキュラム構成
-
- 工程分析とは
- 工程分析の種類と特徴
- 動作研究とはト
- 動作研究における代表的な分析手法
- 運搬分析(マテハン)とは
- 様々な運搬分析
- まとめ
-
k2-06
アニメで学ぶ“IE入門~IE手法の概要編~”
有料サービス限定
5:作業測定に関する手法の概要
受講対象者
現場部門, 間接部門, 主任・班長クラス, 係長クラス, 課長クラス- カリキュラム構成
-
- ①時間研究とは
- 時間研究の種類
- ②稼働分析とは
- 稼働分析の活用場面
- 稼働分析の代表的な手法
- まとめ