工程分析とは?工程分析のステップや流れ線図(フローダイアグラム)について解説
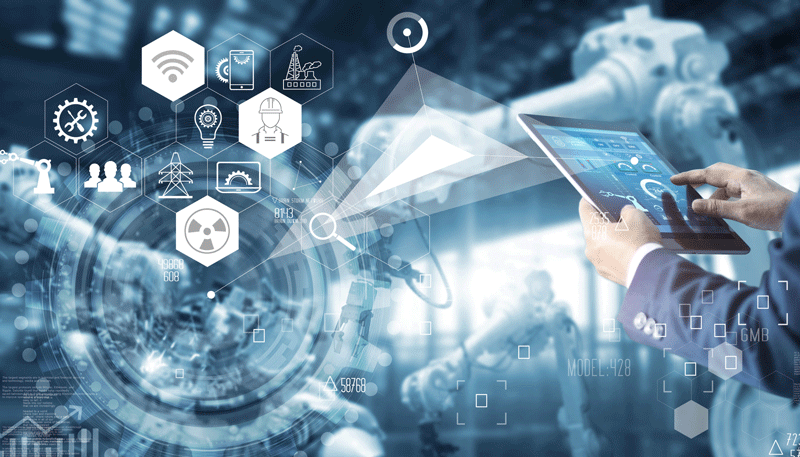

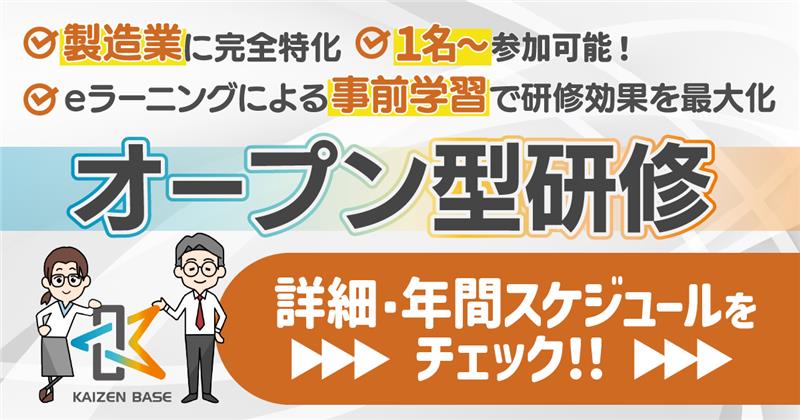
目次
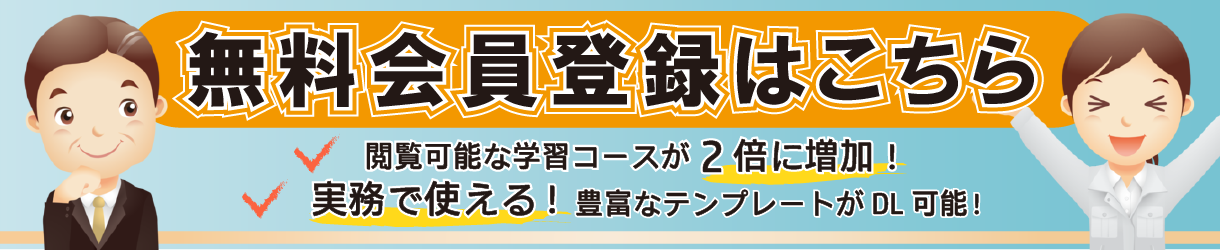
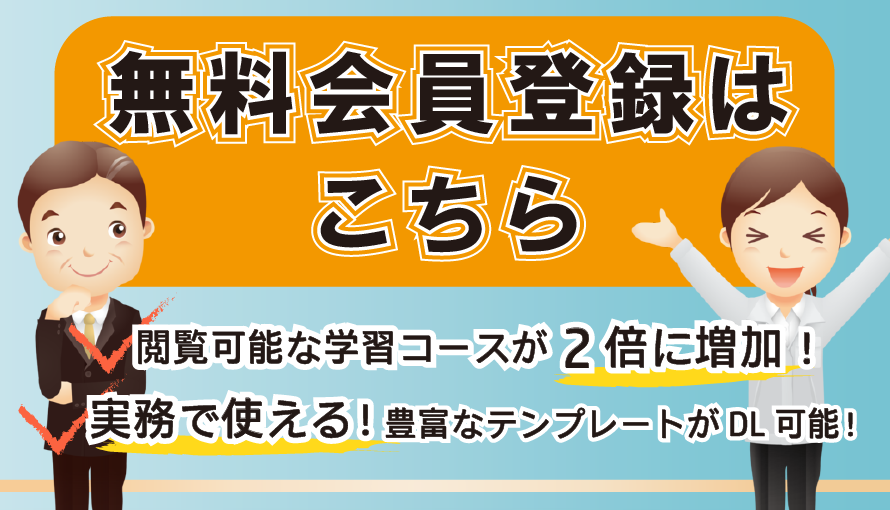
工程分析(こうていぶんせき)とは
工程分析の定義
工程分析とは、各工程のモノの流れあるいは人の仕事の流れを一定の記号で図表化することで問題点を見つけるための分析のことです。IEにおける「方法研究に属する手法」の1つとして位置付けられています。
ちなみに工程とは、ある段階から次の段階へと進むにつれて完成(又は完了)に近づいていく区切りのことを指します。生産や事務作業の流れには様々な順序がありますが、一定の切り口で区切ることで、仕事の段取りや管理がしやすくなります。
工程分析により、作業の流れや手順の全体像を把握することが出来ます。
従って、より詳細な手法を適用する前の予備調査として活用されることが多いのが、この工程分析です。本ページでは、工程分析の定義や考え方、工程分析の種類(単純工程分析、詳細工程分析、流れ線図)そして実際の分析のステップについて解説をしています。
工程分析は方法研究に属する手法の1つ
それではここから、工程分析の概要・種類と分析のイメージについて確認していきたいと思います。
工程分析の種類と特徴
工程分析には、いくつかの種類があります。特徴と合わせて確認しましょう。
1つ目は、単純工程分析です。「作業」と「検査」の系列だけを対象として、工程の流れや状態を分析する方法です。
2つ目は、詳細工程分析です。「作業」と「検査」に加え「移動・運搬」や「手待ち・停滞」「保管・貯蔵」などの状態も含めて分析する方法です。
なお、詳細工程分析には2種類あります。
1つは製品工程分析で、モノを中心に分析を行なう方法で、もう1つは作業者工程分析で、作業者を中心に分性を行なう方法です。詳細工程分析に関しては、第2章で詳しく学習を行ないます。
3つ目は、連合作業分析です。人と機械・人同士の組み合わせ作業に対して、時間的の経過の面から関連を分析する方法です。連合作業分析は、動作研究や時間研究の内容も含まれてくるため、別講座「方法研究と作業測定を組合せた応用的手法」で詳しく学習を行ないます。
4つ目は、運搬経路分析です。流れ線図とも言います。各レイアウトに対してモノまたは人の移動経路を線図にまとめて分析する方法です。
工程分析の活用シーン
工程分析の具体的な活用シーンは、次の通りです。
・より詳細な分析に先立って、工程全体の流れを把握するため
・改善を行なう際に、重点的に取り組む工程を特定するため
・レイアウト改善、運搬改善のための現状調査のため
・リードタイム短縮のための現状調査のため
・工程設計や工程編成の基礎資料として活用するため
これらのシーンがあった時は、「あ、工程分析が使えるな」とすぐに思えるようになったらバッチリですね。
工程分析図(プロセス・チャート)とは
それでは次に、工程分析図(プロセス・チャート)とは何か確認していきましょう。
3種類のプロセス・チャート
工程分析では、工程分析図(プロセス・チャート)を作成します。これは、工程の流れを体系的に図表化したものです。
今回この講義で学習するプロセス・チャートは、次の3種類です。
1つ目は、単純工程分析(オペレーション・プロセス・チャート)です。生産工程のプロセス全体を一目で把握できることが特徴です。
2つ目は、詳細工程分析(フロー・プロセス・チャート)です。オペレーション・プロセス・チャートによりも詳細に工程を分析できることが特徴です。
3つ目は、運搬経路分析(フロー・ダイアグラム、流れ線図)です。フロー・プロセス・チャートに加えて、人とモノの動線も一緒に見ることができるのが特徴です。
プロセス・チャートのイメージ
それぞれのプロセス・チャートのイメージは、ここに示す通りです。
オペレーション・プロセス・チャートは、大まかな工程の流れの分析であることが分かると思います。
フロー・プロセス・チャートは、詳細をしっかり分析であることが分かると思います。
フロー・ダイアグラム/流れ線図は、レイアウト上に流れを記載することで視覚的に分かりやすくした分析であることが分かると思います。
工程分析と言っても、1つの種類ではなく、何を分析したいのか?どういう効果を得たいのかによって、選択すべきプロセス・チャートを分けなければいけません。本講義を通して、分析の目的に応じて適切なプロセス・チャートや図が活用できるようなスキルを身に付けていきましょう!
工程分析記号
それでは工程分析記号を確認していきます。全部で6種類の記号を使用します。
まずは加工です。〇型の記号で表します。加工には、作業や操作も含まれます。原材料や部品、仕掛品や製品の形状や性質に変化を与えている工程(付加価値を与えている工程)が該当します。
次は検査です。検査には2種類あり、1つは数量検査で、□型の記号で表します。原材料や部品、仕掛品や製品の形状や性質に変化を与えている工程(付加価値を与えている工程)が該当します。もう1つは、品質検査で、◇型の記号で表します。原材料や部品、仕掛品や製品の品質を確認し、基準に対して合格/不合格を判定する工程(品質検査工程)が該当します。
4つ目は運搬・移動で、矢印型の記号で表します。原材料や部品、仕掛品や製品の位置に変化を与えている工程(モノを移動させている工程)が該当します。
最後に停滞です。停滞にも2種類あり、1つは滞留で、D型の記号で表します。原材料や部品、仕掛品や製品が加工・運搬・検査もされずに停滞している状態が該当します。もう1つは貯蔵・保管で、逆三角形型の記号で表します。原材料や部品、仕掛品や製品を計画よりも多く貯えている状態が該当します。
以上の6つとなります。なお、それぞれの記号において、負荷価値を生んでいる作業はどれか分かりますか?
そう、加工だけになります。検査、運搬・移動は付随作業、停滞はムダに分類されます。検査作業に関しては、価値作業に分類することがありますが、これは、顧客から認められた検査であり、その検査の対価としての金額を受け取れる場合のみとすることが多いと覚えておきましょう。
プロセス・チャートで分析を行なった結果、付随作業やムダの記号が多い場合は、改善の余地が大きいと判断することができますね。
工程分析の複合記号
以上で説明した6つの記号を組み合わせた複合記号を使うこともあります。いくつか事例を紹介しましょう。
加工を主として行いながら、数量検査も同時にを行う場合は、〇の中に□の記号で表します。モノを手に取った時に数も一緒に数える時などが該当しますね。
加工を主として行いながら、運搬も同時に行う場合には、〇の中に矢印の記号で表します。作業をしながらモノの場所を動かす時などが該当しますね。
数量検査を主として行いながら、品質検査も同時に行う場合には、□の中に◇の記号で表します。
品質検査を主として行いながら、数量検査も同時に行う場合には、◇の中に□の記号で表します。
これらの複合記号は、主となる方が外側、副人なる方が内側と覚えておけばよいですね。
なお、これらの複合記号は、主となるもので判断します。ここに挙げている複合記号の場合、価値作業、価値作業、付随作業、付随作業となりますね。
工程分析のイメージ
では、工程分析のイメージについて確認してみましょう。例として、パレティーナから製品を取り出し、検査台の上で検査をして、検査後にトレーに入れるという流れを対象にしてみます。
この作業における工程分析は、次のようになります。
『パレティーナ内で待機⇒製品取り出し⇒検査台へ移動⇒品質検査⇒トレーへ移動⇒トレーへ製品収納⇒トレー内で待機』
このように、工程分析の基本は、作業を工程分析記号を用いて順番に並べていくだけです。このように並べてみると、付加価値を付けている工程が何個あるか、移動や停滞がどのくらいあるか等を数値で判断できるようになります。基本はこの考え方であり、決して難しいものではありません。苦手意識を持たないようにしましょう。
工程分析における改善の着眼点
では、それぞれの工程に対する着眼点を確認してみます。
加工(作業、操作)に関しては、
・そもそも加工・作業を無くせないか、他の仕事と一緒に出来ないか
・工程順序を変えられないか、材料・機械・人を変えたら改善しないか
・連合作業分析や動作研究など他の手法で改善出来ないか
等が着眼点です。
検査に関しては、
・そもそも廃止できる検査は無いか
・ポカヨケや治具を使って簡素化出来ないか
・加工や運搬工程で同時に出来ないか
・検査基準は適正か、過剰な基準ではないか
・連合作業分析や動作研究など他の手法で改善出来ないか
運搬・移動に関しては、
・運搬(移動)を無くせないか、運搬(移動)回数を減らせないか
・運搬(移動)距離や時間を減らせないか
・運搬(移動)中に他の仕事や検査が出来ないか
・レイアウト改善や工場内物流改善により改善出来ないか
滞留に関しては、
・停滞(手待ち)を無くせないか、ゆっくりでも移動させられないか
・停滞(手待ち)回数や時間を減らせないか
・停滞(手待ち)中に他の作業が出来ないか
・レイアウト改善や運搬活性分析により改善出来ないか
貯蔵・保管に関しては、
・そもそも貯蔵は本当に必要なのか
・時間やロット数を減らせないか
・原材料、部品を共通に出来ないか
・貯蔵中を利用して他の作業が出来ないか
・レイアウト改善や工場内物流改善により改善出来ないか
等が着眼点です。
プロセス・チャートを作成した後は、これらの着眼点を参考にしながら改善を進めていくことになります。
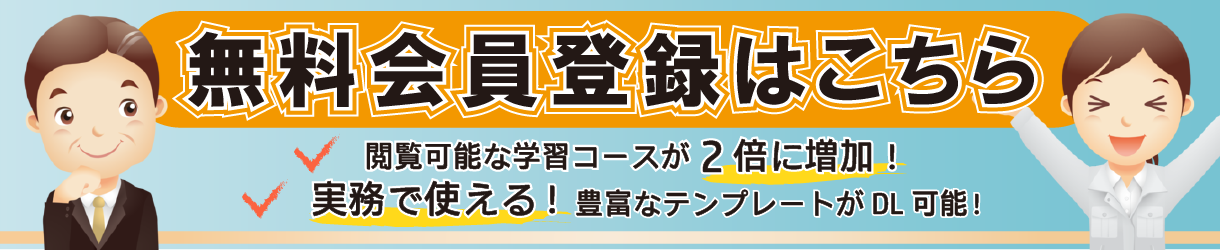
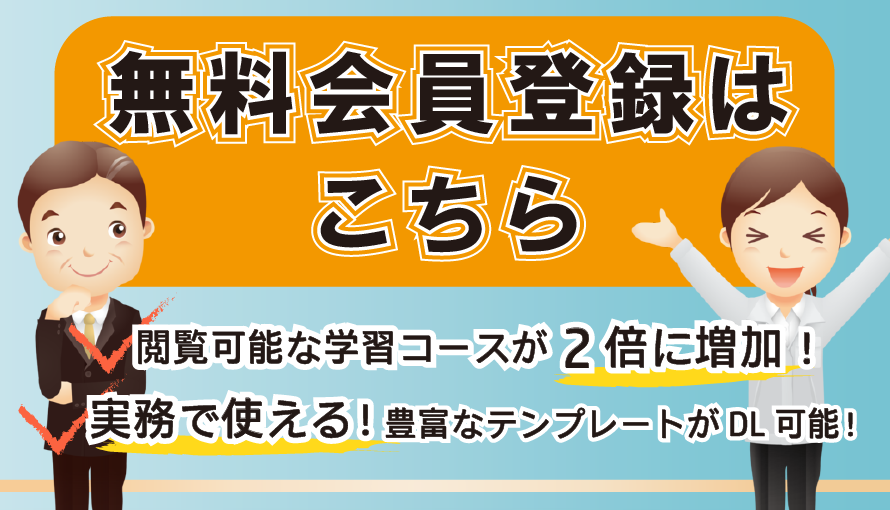
単純工程分析とは
加工と検査に着目する単純工程分析
それでは次に、単純工程分析とは何か確認していきましょう。
単純工程分析とは、加工と検査の2つにのみ着目する方法です。
運搬や停滞等は無視し、どのような作業、検査を行なっているかという、工程全体の概略を掴むことが目的です。
生産工程のプロセス全体を一目で把握できる
単純工程分析図は、オペレーション・プロセス・チャートとも呼ばれ、ここに示すような形で作成されます。
特徴として、生産工程のプロセス全体を一目で把握できることが挙げられます。
ここでワンポイントです。単純工程分析図(オペレーション・プロセス・チャート)では、分析の目的に応じて、所要時間、位置等、その他の情報を記入するようにしましょう。書いてはいけないものはありません。必要なものは独自に追記し、自分たちにとって工程全体が一目で分かりやすいものを作成するようにしましょう。
単純工程分析図(オペレーション・プロセス・チャート)の活用シーン
単純工程分析図(オペレーション・プロセス・チャート)は次のようなシーンで活用されます。
- 詳細工程分析の前段階として全体を掴むために活用する
- 新製品や既存製品の工程の全体像・流れを可視化し、QC工程図等へ活用する
- 原材料や部品の搬入と各工程との関連を確認する
- 全工程数や各工程の工数を把握し、各種見積もりに活用する
QC工程図で見たことがある方も多いかもしれませんね。
単純工程分析の進め方
それでは次に、単純工程分析の進め方について確認していきましょう。
単純工程分析のステップ
単純工程分析は、次のステップで進めていきます。
① 目的を明確にする
②対象を決める
③ 調査時期や方法を決める
④オペレーション・プロセス・チャートへまとめる
それではオペレーション・プロセス・チャートの描き方を確認します。
単純工程分析図(プロセス・チャート)の描き方
単純工程分析図(プロセス・チャート)の描き方は次の通りです。
まず、タイトルを書きます。何の単純工程分析図なのか、後から見て分からなくならないように、誰でも分かるタイトルを書きましょう。
次に、必要事項を書きます。工程名、品名、作成日、作成者等を記載します。
次に、メインの工程の流れを描きます。
そして、メインの流れに合流する材料や工程の流れを描いて合わせていきます。
流れの各工程に対して、必要に応じて所要時間などを記載しましょう。
工程の合流、分岐の描き方
ちなみに、工程の合流、分岐の描き方にも決まりがあります。
組み立て生産方式では、このように、線の上に合流・分岐させる描き方をします。
一方、装置生産方式では、このように、記号に合流・分岐させるような描き方をします。
また、手直し合流がある場合は、このような描き方をします。基本的にはフローチャートのような図を順番に描いていくだけなので、あまり難しく考えずに、「まずは描いてみる」ことが大切です。
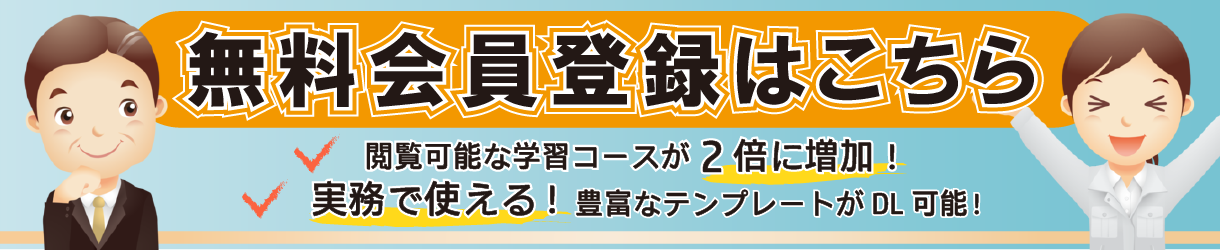
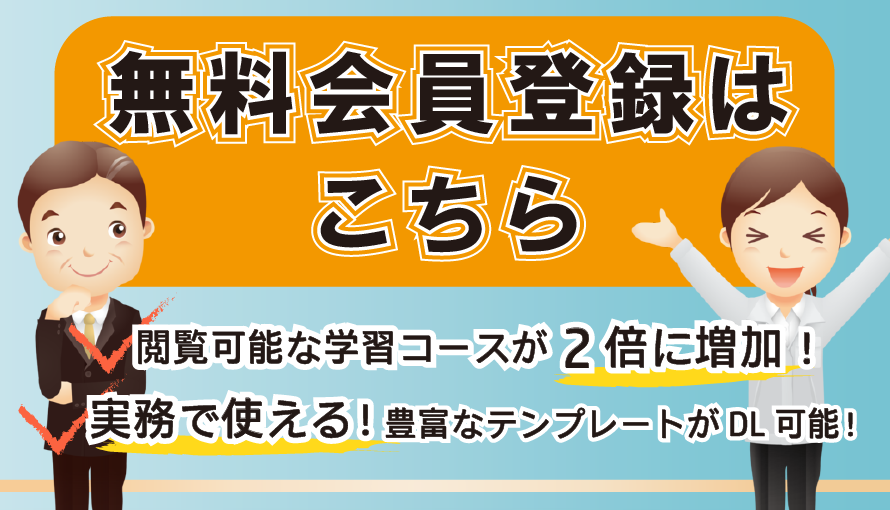
詳細工程分析(製品工程分析・作業者工程分析)とは
それでは次に、詳細工程分析とは何か確認していきます。
詳細工程分析図(フロー・プロセス・チャート)とは
詳細工程分析図は、フロー・プロセス・チャートとも呼ばれる手法です。詳細工程分析図(フロー・プロセス・チャート)は、スライドに示すようなチャート図になります。原材料・部品から製品に至る生産工程の全貌を詳細に把握できることが特徴です。
ここでワンポイントです。詳細工程分析はその名の通り、詳細な分析を行ないたい時に有効な手法です。一方単純工程分析は、工程の全体像を大まかに掴むことが目的でした。
実際の使い方としては、単純工程分析で問題になる工程を特定し、その工程に対して詳細工程分析を行っていく形が基本です。もし全ての工程を詳細に分析しては、手間も掛かり、逆に問題が見えにくくなってしまうからです。
従って、単純工程分析である程度対象を絞った上で詳細分析を行なう方が合理的な進め方であると覚えておきましょう。
詳細工程分析は2種類に分けられる
詳細工程分析は2種類に分けられることも既に学びました。何と何か覚えていますか?
そう、製品工程分析と作業者工程分析の2つです。
製品工程分析は、工程の詳細を「モノ」の動きの視点から分析する方法です。
一方、作業者工程分析は、工程の詳細を「ヒト」の動きの視点から分析する方法です。
製品工程分析と作業者工程分析の使い分け
さて、モノの視点とヒトの視点から分析すると言いましたが、実際にはどう使い分けたらよいのでしょうか?
使い分けのイメージとしては、このように考えましょう。
まず、製品工程分析は、
・モノの動線を知りたい・改善したい時
・リードタイムを知りたい・短縮したい時
・レイアウトを改善したい時
等に活用します。動線・リードタイムが特に重要なキーワードです。
一方、作業者工程分析では、
・作業者の動線を知りたい・改善したい時
・みずすまし・段取り作業者・リフト作業者等の動きやパターンを知りたい・改善したい時
等に活用します。特に、繰り返し作業を行なっていない付帯作業者は、普段どのような動きをしているか見えにくいことがあります。
そんな時は、作業者工程分析を行ない、実情を把握し改善するアプローチをすると効果的です。
詳細工程分析は運搬・移動・滞留等をしっかりと分析できるかが鍵
工程分析図を作成する際には、第1章で学習したこれらの分析記号を全て使って行います。全体像を把握する単純工程分析とは異なり、運搬・移動・滞留等をしっかりと分析できるかが鍵になります。
詳細工程分析の進め方
それでは次に、詳細工程分析の進め方について確認していきましょう。
工程分析のステップ(Step1,2)
工程分析のステップは、次の5つです。
Step1:工程分析を行う目的を明確にする
目的を明確にしなければ分析が中途半端になってしまうこともよくあります。
目的を明確にし、分析の要点・調査項目等を要領よく確実に素早く的確に分析することが大切です。
ここでワンポイントです。
既に解説したように、工程分析においては適切な種類の手法を選定しなければなりません。
例えば、工程全体の工数を減らしたいのであれば単純工程分析、レイアウトの改善を行ないたいのであれば製品工程分析、作業の改善を行ないたいのであれば作業者工程分析というように、目的に応じて的確なツールを使うようにしましょう。
Step2:工程分析の対象範囲を決める
どの工程からどの工程まで分析する必要があるのか、分析の目的を考慮して決定するようにしましょう。
あまりに対象範囲が広いと、分析だけで相当な時間が掛かってしまいます。
しっかりと目的を考え、必要な範囲で分析を行なうことがポイントです。
ここでワンポイントです。
詳細工程分析を行なう時には、例えば、「部品ピッキングから完成品の保管まで」 「他部署との引き渡し場所まで」等のように、対象範囲を明文化しましょう。
曖昧に進めてしまい、分析漏れや過剰な分析工数が発生してしまうことは避けるようにしてください。
Step3:分析対象となる製品・作業を決める
現代では多品種の生産をしていることがほとんどであり、分析となる工程で流れる製品や作業の種類は、複数パターンあることが普通です。
特定製品のみを対象にするのか、ある製品群を対象にするのか等、対象を明確化するようにしましょう。
対象を選定する際には、P-Q分析を実施し、生産量が上位の製品を特定する等の考慮が必須です。
ここでワンポイントです。
IE・インダストリアルエンジニアリングの概要で解説した、P-Q分析という言葉は覚えていますか?
P-Q分析とは、横軸に品目(Product)、縦軸に生産量や出荷量(Quantity)をとり、生産品目を量の多い順に並べて比較したグラフです。
優先順位を付けて分析対象を決める際に有効な方法として覚えておきましょう。
工程分析のステップ(Step4)
Step4:工程分析表を作成する
調査した距離と時間のデータ等を正しく記入します。
距離や時間は正確であることに越したことはないものの、100%厳密でなくても概ね正しければ構いません。
ここでワンポイントです。
例えば、1単位を数回に分けて運搬する場合は、
(1回の運搬距離×運搬回数)/総運搬距離というように、後から検討しやすいように区別して記載しておくと便利です。
工程分析シートの作成方法は、次節にて確認しましょう。
工程分析のステップ(Step5)
Step5:改善案を検討する
ここに示すような総括表を活用し、「加工」や「作業」以外の数の削減や時間の削減を行ないます。
特に意識するのは、運搬、待ち、貯蔵です。これらをどのくらい減らすことが出来るかが改善のポイントです。
改善検討のための視点には様々あります。
第3章で学ぶ「流れ線図」もその1つで、レイアウト図に動線を描き、人やモノのムダな動きを分析する手法です。
動作研究の講座で学ぶ「動作経済の原則」も改善の着眼点として有効です。
人間にとって無理なく最適な方法への改善をするための視点です。
ECRSの原則も代表的なフレームワークとなります。
改善効果の高い方から、排除、結合、交換、簡素化という順で改善案を検討します。
6W2Hも同様に有効です。
Why、What、When、Where、Who、Whom、How、How muchの視点から改善案をモレなく洗い出す方法です。
これらの視点を上手く活用し、様々な改善案を挙げることで工程を改善していきます。
詳細工程分析表の作成方法
それでは次に、詳細工程分析表の具体的な作成方法について確認していきます。
「モノの動き」の視点か「ヒトの動き」の視点で分析
詳細工程分析では、「モノの動き」の視点で分析するか、「ヒトの動き」の視点で分析するかにより使用する帳票が若干異なります。
とは言え、「加工」と「作業」、「停滞」と「待ち」という表現の違いがあるくらいで、基本的な進め方は同じです。なぜ違うかというと、「モノは加工される」「ヒトが作業する」という違い、「モノが停滞する」「ヒトが待ち状態にある」という違いです。意味合いとしてはほぼ同じですが、分かりやすいように分けているということです。
製品工程分析シートの作成例
では、詳細工程分析表の作成方法を製品工程分析シートを例に確認していきます。
まずは、基本情報を書きましょう。どの工程を対象にしたのか、対象の製品名は何か、作成日はいつか、作成者は誰か、改善前の分析シートか改善後か等の情報を記載します。
次に、作業内容を書き出します。モノ(製品)の視点から作業内容(モノの流れ)を書き出していきましょう。
ここでワンポイントです。
作業内容の項目は、可能な限り、「〇〇の〇〇」「〇〇を〇〇する」というように、何をどうする、何がどうなるというのが誰にでも分かりやすいように記載しましょう。「移動」だけしか書いていないと、後から見た時にどこへ移動したのか分からなくなってしまうためです。
初期のうちは経験者に作成したシートを見てもらおう
次に、各作業内容が、加工、運搬、検査、停滞、貯蔵のどの区分に分類されるか判断し印を付けていきます。
そして、距離・数量・時間の情報として、何メートル運んだのか、何個ずつ運んだのか、何分時間が掛かったのか等を記載していきます。
ここまで作成できれば、現状の把握が完了です。初期のうちは、経験者に作成したシートを見てもらい、自分の分析の精度がよいか指導を仰ぐようにしてください。
問題の明確化と改善の着眼点の検討
現状把握ができたら、問題の明確化と改善の着眼点の検討を行なっていきます。目的、場所、順序、作業者、方法の視点から、問題の着眼点の区分をチェックしていきましょう。
更に、やめる、減らす、統合、変える、簡素化の視点から、改善の着眼点の区分をチェックします。
そして、真ん中の部分に問題点や改善点を記載していきます。
ここでワンポイントです。
工程分析において改善案を検討する際には、まずはたくさん改善案を洗い出し、その後優先順位を付けて進めていくようなアプローチが有効です。「これは出来ない」「それは難しい」というのはNGワードとして進めていきましょう。
分析結果のまとめと総括表の作成
最後に、分析結果のまとめとして、総括表を記載します。分析した結果を集計する目的は、各記号が何回発生したのか、どのくらい時間が掛かったのかを一覧で分かるようにするためです。
最後にワンポイントです。
今回例で出しているシートの時間は「分」を使っていますが、実際に分析を行なう場合には、工程の特徴を考慮して、時間の単位を「時間」「分」「秒」のどれにするか判断するようにしましょう。1サイクルが数分の作業に「分」では粗すぎます。何時間もかかる作業に「秒」では細かすぎます。この時間のメッシュをどのくらいにするかは、適切な単位を選定できるセンスを身に付けるようにしてください。
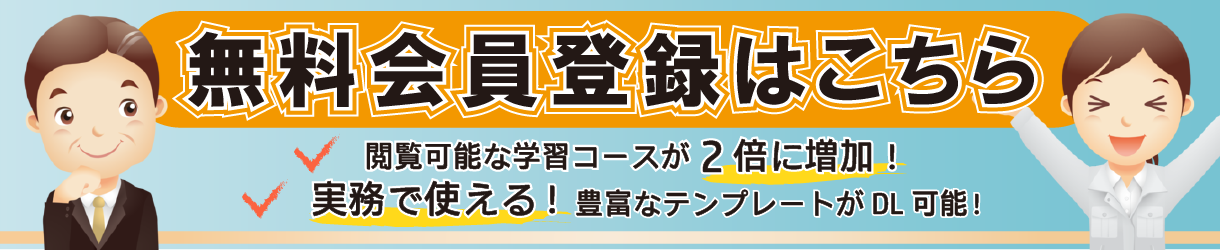
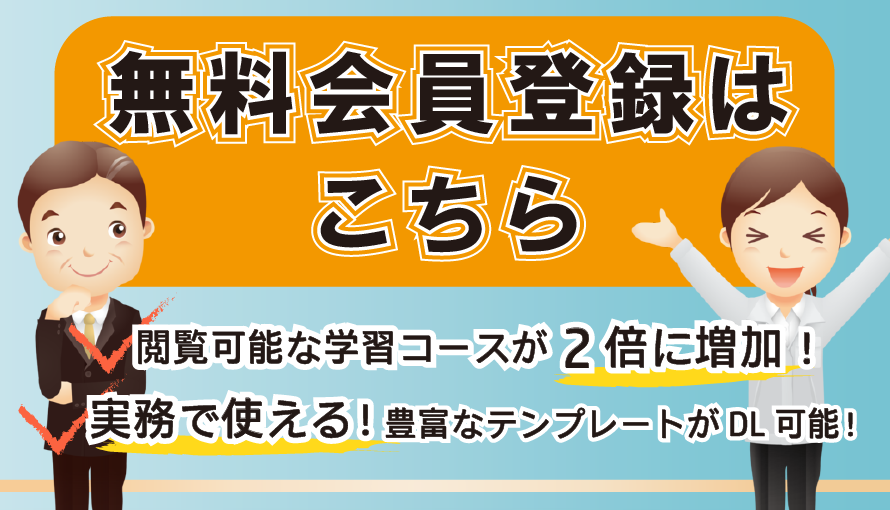
流れ線図(フローダイアグラム)とは何?
流れ線図(フローダイアグラム)とはどんな手法?
流れ線図(フローダイアグラム)は、詳細工程分析図(フロープロセス・チャート)をレイアウト図に落とし込み、人やモノのムダな動き・動線を分析するための手法です。
流れ線図(フローダイアグラム)は、工程分析において動線が重要な要因となる場合に、詳細工程分析図と一緒に作成されます。
同じ経路の往復の存在、余分な歩行や運搬、人やモノの動きが激しく混雑する地点などが動線として確認できるので、レイアウトの改善方向などが一目で明らかになります。
流れ線図のイメージはここに示す通りです。人やモノがどのようなルートで動いているのかをレイアウト上に動線として記載していくことで、ムダを明らかにしていきます。
流れ線図の作り方
流れ線図作成においては、まずはレイアウト図を用意します。
Excelのオートシェイプ機能で作成したものや、手書きで作成したものでも構いません。
もちろん、縮尺や寸法が実際と大きく異なるものや、あまりに雑なものを使ってしまうと、正確な分析ができないので、ある程度正確だと認められるものを使用してください。
次に、基本情報を記載します。職場名、作業名、作成日、作業者を記載します。
次に、用意したレイアウト図をシートに貼り付けましょう。
動線を描き、分析記号や数値を記入する
次に、作業者や製品の動線を描きます。
当然ながら、モノや人の動きを現地現物でしっかりと調査した上で描いていくようにしてください。
何となく感覚で描いてはいけません。
次に、工程分析記号を書き入れます。
運搬の場合は、歩いていく方向に書き入れると分かりやすいですね。
そして、各工程・作業の内容(時間、距離等)を記入していきます。
レイアウト上で動線の近くの分かりやすい場所に書きましょう。
製品工程分析表や作業者工程分析表と一緒に活用しよう!
現状を流れ線図の中に落とし込むことができたら、詳細工程分析表と流れ線図をもとに、改善案を検討していきます。
ここでワンポイントです。
流れ線図だけでも分析は可能ですが、製品工程分析表や作業者工程分析表も可能な限り一緒につくりましょう。
2つを合わせて確認しながら改善案を検討していくことが、より大きな効果を上げるためのコツの1つです。
もう1つワンポイントです。
改善後の動線は赤色にするなど、色を変えて記載すると効果が一目で分かるのでオススメです。
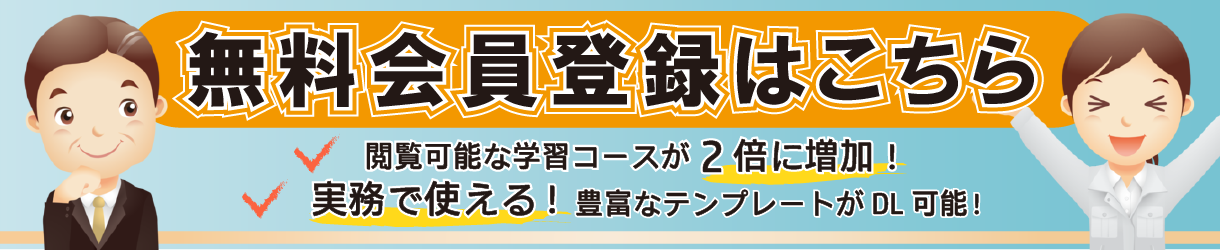
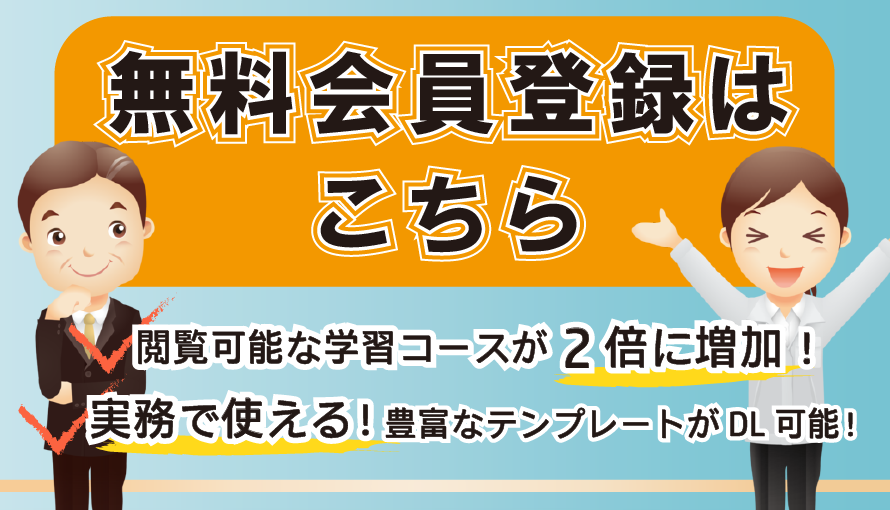
工程分析のまとめ
以上で学んだことをまとめてみましょう。
工程分析とは?
- 工程分析とは、各工程のモノの流れあるいは人の仕事の流れを一定の記号で図表化することで、問題点を見つけるための分析のこと
- 工程分析の種類は、単純工程分析、詳細工程分析、連合作業分析、運搬経路分析の4つ
- 詳細工程分析は、製品工程分析、作業者工程分析の2種類があり、運搬経路分析は流れ線図という呼び方も有名
- 単純工程分析図は、オペレーション・プロセス・チャートとも言う。生産工程のプロセス全体を一目で把握できるのが特徴
- 詳細工程分析図は、フロー・プロセス・チャートとも言う。原材料・部品から製品に至る生産工程の全貌を詳細に把握できることが特徴
- 流れ線図(フローダイアグラム)は、詳細工程分析図をレイアウト図に落とし込み、人やモノのムダな動き・動線を分析するための手法
いかがでしたか?工程分析の概要はイメージできましたか?
IEの中での使用頻度が高い工程分析。分析方法を身に着けて、必要なタイミングで活用できるようにしていきたいですね!
参考文献
・新版IEの基礎(著:藤田彰久 、建帛社、1997年)
・現場実践シリーズ IE7つ道具(著:杉原寛 他 、日刊工業新聞社、1993年)
工程分析について学ぶ!学習コースのご紹介
カイゼンベースの学習コースでは、工程分析に関する具体的な内容を動画や理解度テストにより学習することが可能です。詳細の学習や実践でのご活用をご検討の方は、是非ご活用ください。
学習コース「k2-08:アニメで学ぶ“IE実践編~工程分析 Part1~”」
工程分析とは、各工程のモノの流れあるいは人の仕事の流れを一定の記号で図表化することで問題点を見つけるための分析のことです。工程の全体や、モノの流れをつかむことで、全体像を数字で明らかにすることができます。本講座では、工程分析の実践的な知識の概要について学習していきましょう。
学習コースの詳細
Lesson1:工程分析とは(7:17)
Lesson2:工程分析図(プロセス・チャート)の概要(11:30)
Lesson3:単純工程分析とは(6:21)
Lesson4:詳細工程分析とは(5:24)
Lesson5:流れ線図(フローダイアグラム)とは(6:00)
「Lesson1:工程分析とは」の動画はどなたでもご視聴頂けます。
「Lesson2:工程分析図(プロセス・チャート)の概要」の動画は無料会員登録を行うことでご視聴が可能になります。
学習コース「k2-09:アニメで学ぶ“IE実践編~工程分析 Part2~”」
本講座では、Part1から引き続き、工程分析の実践的な知識について学びます。「詳細工程分析」など、主な3種の分析法の、具体的な実施事例・分析表の作成法などを確認していきましょう。工程の全体・モノの流れから、全体像を数字で明らかにする手法について学んでいきましょう。
学習コースの詳細
Lesson1:詳細工程分析の進め方(8:03)
Lesson2:詳細工程分析表の作成方法(6:47)
Lesson3:製品工程分析の実施事例(7:23)
Lesson4:作業者工程分析の実施事例(4:47)
Lesson5:製品工程分析と流れ線図の活用例(7:38)
「Lesson1:詳細工程分析の進め方」の動画はどなたでもご視聴頂けます。
「Lesson2:詳細工程分析表の作成方法」の動画は無料会員登録を行うことでご視聴が可能になります。
資料請求はこちらから
サービス紹介資料・価格表を無料でダウンロードできます。お気軽にお問い合わせください。

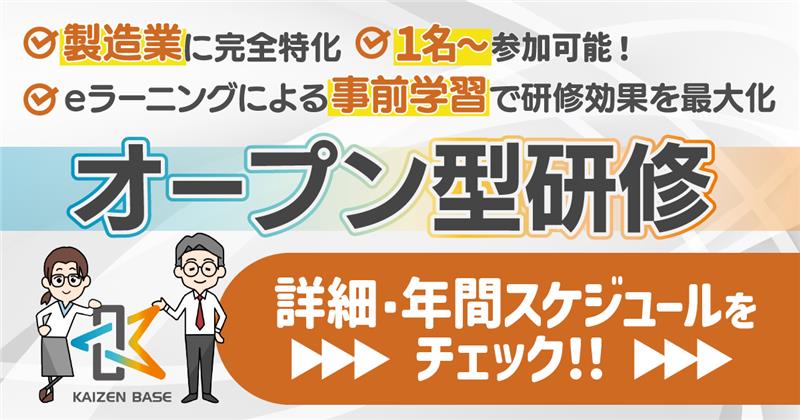
関連学習動画
-
k2-06
アニメで学ぶ“IE入門~IE手法の概要編~”
無料会員限定
2:テーラーとギルブレスの功績
受講対象者
現場部門, 間接部門, 主任・班長クラス, 係長クラス, 課長クラス- カリキュラム構成
-
- IEの父と呼ばれる2人の人物
- テーラー|シャベルすくいの実験を行った人物
- ギルブレス|レンガ積みの研究を行った人物
-
k2-06
アニメで学ぶ“IE入門~IE手法の概要編~”
有料サービス限定
3:IEにおける各種手法
受講対象者
現場部門, 間接部門, 主任・班長クラス, 係長クラス, 課長クラス- カリキュラム構成
-
- IEにおける各種手法
- IE(≒作業研究)は大きく2つに分類される
- 方法研究と作業測定を組み合わせた応用的な手法
- 各種手法の活用シーン
- まとめ
-
k2-06
アニメで学ぶ“IE入門~IE手法の概要編~”
有料サービス限定
6:組み合わせ手法の概要
受講対象者
現場部門, 間接部門, 主任・班長クラス, 係長クラス, 課長クラス- カリキュラム構成
-
- ①連合作業分析
- ②ラインバランス分析
- ③プラント・レイアウトト
- 各分析手法の位置づけを生産の流れ
- まとめ
-
k2-06
アニメで学ぶ“IE入門~IE手法の概要編~”
有料サービス限定
5:作業測定に関する手法の概要
受講対象者
現場部門, 間接部門, 主任・班長クラス, 係長クラス, 課長クラス- カリキュラム構成
-
- ①時間研究とは
- 時間研究の種類
- ②稼働分析とは
- 稼働分析の活用場面
- 稼働分析の代表的な手法
- まとめ
-
k2-06
アニメで学ぶ“IE入門~IE手法の概要編~”
有料サービス限定
4:方法研究に関する手法の概要
受講対象者
現場部門, 間接部門, 主任・班長クラス, 係長クラス, 課長クラス- カリキュラム構成
-
- 工程分析とは
- 工程分析の種類と特徴
- 動作研究とはト
- 動作研究における代表的な分析手法
- 運搬分析(マテハン)とは
- 様々な運搬分析
- まとめ
-
k2-06
アニメで学ぶ“IE入門~IE手法の概要編~”
公開講座
1:IE・インダストリアルエンジニアリングとは
受講対象者
現場部門, 間接部門, 主任・班長クラス, 係長クラス, 課長クラス- カリキュラム構成
-
- IEとは
- IE手法活用の1番の狙い
- IEのメリット
- まとめ