トヨタに学ぶ「なぜなぜ分析」の真髄:現場で活かす根本原因追求法と実践ヒント
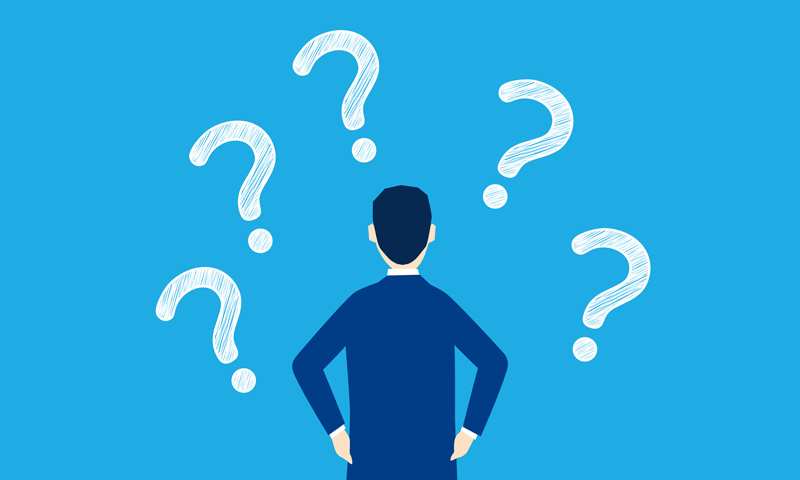
.png)
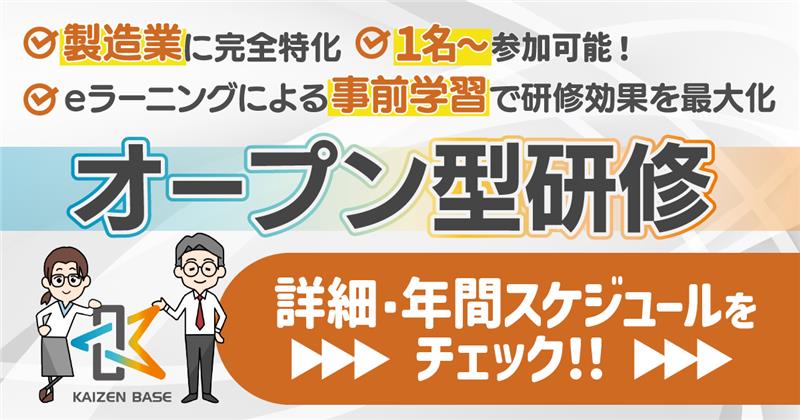
目次
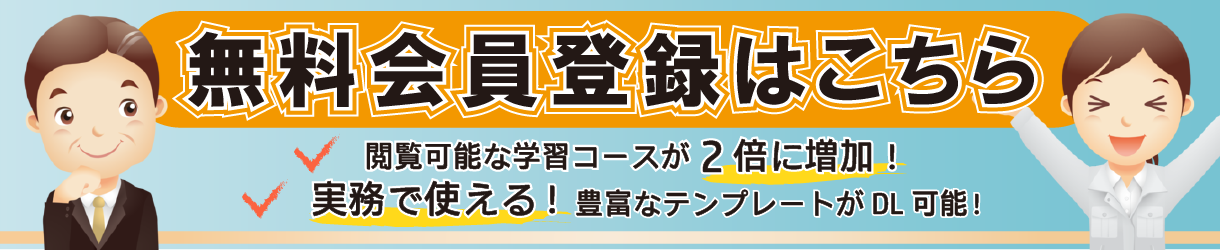
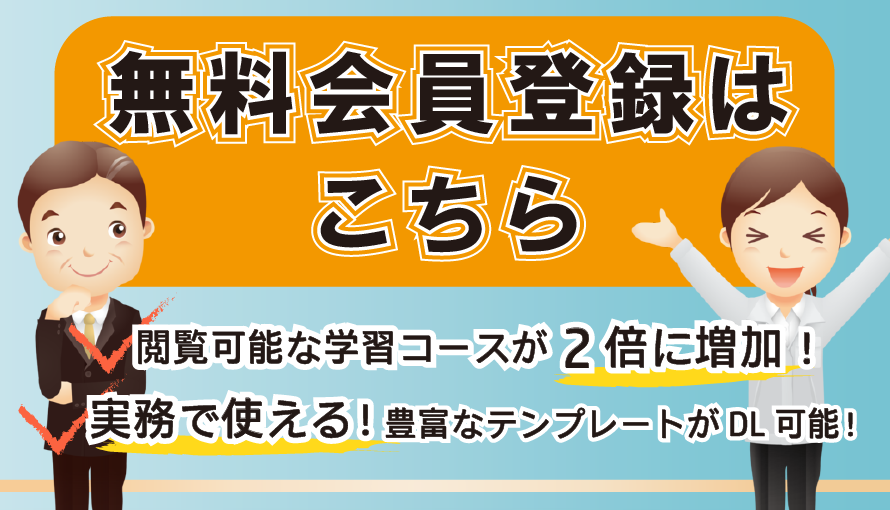
なぜなぜ分析は、日々の業務、改善活動では欠かせない問題解決の技術です。
本ページでは、なぜなぜ分析の考え方、進め方について解説をしています。なぜなぜ思考で考える力を付け、日々の業務における問題解決力を上げていきましょう。
「なぜ」を5回繰り返したら何が見えたか? – トヨタの現場エピソード
ある自動車工場で機械が突然停止するトラブルが発生しました。通常ならヒューズを交換して機械を再稼働させるだけで終わっていたかもしれません。しかし、その現場担当者は問題の再発を防ぐため、原因を徹底的に追究することにしました。彼は発生原因を探るべく、「なぜ機械が止まったのか?」と問いかけます。ヒューズが切れたからだと分かると、さらに「なぜヒューズが切れたのか?」と続けました。このように「なぜ?」を繰り返し問いかけていくと、次第に故障の背後に潜む原因が明らかになります。
5回の問いを通じて原因を深掘りすると、最終的には「ストレーナー(濾過器)が付いていないので切粉(金属粉)が内部に入り、潤滑ポンプが故障して十分に潤滑できず、オーバーロードでヒューズが飛んだ」という真因にたどり着きました。対策として「ストレーナーを取り付ける」ことが導き出され、問題の根本解決に結びついたのです。もし表面的な原因で止めてヒューズの交換だけで済ませていたら、また同じトラブルが数ヶ月後に再発していたでしょう。このエピソードは、トヨタで実際に行われた有名な事例であり、「5回のなぜ」と呼ばれる手法の威力を物語っています。
このようになぜを繰り返すことで真因を突き止め、再発防止につなげる問題解決法を、トヨタでは古くから重視してきました。しつこいくらいに「なぜ」を問い続けることで真因に直接アプローチできる解決策が見つかり、同じ問題に二度と悩まされなくなるからです。一般的に「5回繰り返せば大抵の原因に行き着く」とされ、トヨタの大野耐一氏もこの「5回のなぜ」を現場指導で用いたことで知られています。もちろん問題によっては5回で足りない場合もありますが、重要なのは問題の本質に届くまで粘り強く問い続ける姿勢です。これこそがトヨタ発祥の「なぜなぜ分析」の真髄であり、現場のカイゼン(改善)を支える強力なアプローチなのです。
なぜなぜ分析とは何か?その定義と目的
「なぜなぜ分析」(5 Whys分析)とは、発生した問題の根本原因(真因)を明らかにし、再発防止の対策を講じることを目的とした分析手法です。問題やトラブルに直面した際に「なぜ?」という質問を繰り返しながら原因を深く掘り下げていき、表面的な要因ではなく背後にある真因を特定します。トヨタ自動車の元副社長である大野耐一氏が提唱・実践したことで広まり、トヨタ生産方式(TPS)を構成する手法の一つとして有名になりました。実際、トヨタは問題解決の際に徹底して「なぜ」を繰り返し、原因を根本から解決する文化を育んできています。この手法を用いることで、一時しのぎの対応に終わらず再発防止につながる真の解決策を見出すことが可能になります。
さらに、このプロセスには職場のメンバー全員が自由に発言し、多面的な視点で議論に参加できるという特徴もあります。現場担当者、技術者、管理者が垣根なく「なぜ?」をぶつけ合うことで、組織内のコミュニケーションが活性化し、チーム全体の問題解決力が高まります。このように職場の協力体制を強化しながら根本原因を究明するプロセスそのものが、現場の改善文化を育てる土壌になります。「なぜなぜ分析」は単なる問題解決ツールに留まらず、組織全体に改善(カイゼン)の文化を醸成し、より良い製品やサービスを生み出すための基盤となる考え方だと評価されています。
トヨタ発祥のこの分析手法は、生産現場を中心に広く活用されてきましたが、そのシンプルさゆえに製造業以外の業界や日常生活でも応用されています。たとえばIT業界や医療現場、サービス業の課題解決にも役立てられており、問題の本質に迫る汎用的なフレームワークとして認知されています。要するに「なぜなぜ分析」とは、「なぜ?」を繰り返すことで問題の核心を突き止め、再発を防ぐための持続的な改善策を導き出す手法なのです。
現場で徹底追求することの意義とメリット
現場で問題が起こったとき、目の前の不具合をとりあえず直すだけで終わらせてしまうケースは少なくありません。しかし、同じ問題が再び起きれば生産ロスや品質低下につながりかねません。トヨタが示すように、問題の再発防止には問題を引き起こした真因を見つけ出すことが不可欠です。なぜなぜ分析を実践すれば、再発防止によってトラブル対応に費やす時間や労力を大幅に削減でき、生産性や業務効率の向上にもつながります。
また、なぜなぜ分析は特別な専門知識がなくても誰でも取り組める点も大きなメリットです。他の高度な分析手法と異なり、現場・現物・現実の「三現主義」に則った事実の観察からスタートできるため、現場の作業者でも比較的容易に始められるのです。実際に現物を見て、ありのままの現実を確認しながら要因を洗い出していくので、机上の空論ではない確実な原因追及が可能となります。
なぜなぜ分析の基本手順【現場での進め方】
実際に現場でなぜなぜ分析を行う際の基本的な手順を整理しておきましょう。問題発生から対策の実行・検証まで、一連の流れを踏むことで効果的に根本原因へアプローチできます。以下のステップに沿って進めるのが一般的です。
- 問題の明確化・定義: 最初に扱うべき課題を具体的に定義します。何がどのように問題なのかをはっきりさせ、現象を事実ベースで記述します。例えば「不良品が出た」ではなく「○○工程で製品Aに傷不良が発生した」のように、発生した現象を5W1Hで具体化して把握します。問題が曖昧なままだと深掘りができないため、ここを丁寧に行うことが重要です。
- 現状の把握と「なぜ?」の追究: 現場で起きている事実を集めつつ、「なぜ?」という問いを繰り返して原因を深堀りします。まず最初の「なぜ?」で直接原因(一次要因)を特定し、その答えに対して再び「なぜ?」と問いかけて二次要因を探ります。このプロセスを真因に行き着くまで繰り返します。各「なぜ」に対する答えは事実に基づき、前後の因果関係が論理的に繋がっていることを確認しながら進めます。必要に応じて現場・現物を確認し(現地現物主義)、思い込みや仮定で原因を決めつけないよう注意します。一般には5回程度問いを重ねますが、問題によっては適切な回数まで繰り返す柔軟さも必要です。
- 真因の特定と対策立案: 「なぜ?」の追究を通じて浮かび上がった根本原因に対して、有効な改善策を検討・実行します。見つかった真因ごとに再発防止策を考え、実行可能な計画を立てます。対策は現場のメンバー全員が無理なく実行できる現実的なものであることが重要です。例えば真因が「作業手順書が不備」であれば手順書の改訂や教育を行う、設備の問題であれば改善策を設備管理計画に組み込む、といった具合に具体策に落とし込みます。
- 効果検証と標準化: 対策を実施した後は、一定期間経過後に効果検証を行います。不良やミスが再発していないか、品質や生産性が向上したかなどをチェックし、必要に応じて追加の対策や是正を行います。再発防止策が有効であれば、その取り組みを標準手順や教育に組み入れて横展開(水平展開)し、他の現場や類似ケースにも適用します。こうしてPDCAサイクルを回すことで、単発の問題解決を超えて継続的なプロセス改善(カイゼン)へとつなげていきます。
以上が基本的な流れです。一連の手順自体はシンプルですが、実践においては次項のようなポイントを押さえて進めることで、分析の質と効果をさらに高めることができます。
なぜなぜ分析を成功させるためのポイント(現場でのコツ)
なぜなぜ分析を現場で有効に機能させるには、いくつか押さえておくべきコツがあります。以下に、明日から実践できる具体的なポイントを整理しました。現場で分析を進める際は、ぜひこれらを意識してみてください。
- 問題を具体的に絞り込む: 分析の出発点となる課題はできるだけ具体的に定義します。漠然と「品質を向上させる」ではなく、「どの工程のどの製品で何が問題か」を特定しましょう。範囲が広すぎると原因もぼやけてしまうため、まず焦点を当てるべき問題を明確化することが重要です。
- 現場の事実を収集してから分析: 現場(現物)の状況を正確に把握し、データや事実を集めた上で分析を開始します。思い込みや伝聞だけで原因を推測しないように、現場での観察結果や数値データ、当事者のヒアリングなど客観的な情報を下敷きにしましょう。事前に現状をしっかり把握することで、見当違いの「なぜ」に時間を費やすのを防げます。これは三現主義(現場・現物・現実)にも通じる基本姿勢です。
- 「なぜ?」と答えを一対一で繋げる: 「なぜ?」を繰り返す際には、一度に複数の要因を混在させないようにします。一つの問いに対して答えは一つに絞り、出てきた答えに対してまた次の「なぜ?」を問う、という因果のチェーンを一連で繋ぐイメージです。要因を網羅的に洗い出す場合は一つひとつ別の「なぜの連鎖」として分析し、それぞれ因果関係を追究しましょう。同じ問題に複数の根本原因が潜んでいることもありますが、それぞれについて原因追及の筋道を混同せずに整理することが大切です。
- 途中で思考停止しない: 分析の途中で「こんなものだろう」と早合点して終わらせないよう注意します。真因が不明瞭なうちは決して妥協せず、納得できる答えに行き着くまで粘り強く問い続けることが肝心です。ときには5回以上「なぜ」を重ねたり、別の角度から問い直したりする柔軟さも必要です。大切なのは回数にこだわることではなく、真に筋の通った答えが得られたかどうかを判断基準にすることです。
- 原因を人のせいにしない: 原因を特定の個人のミスや注意不足に求めないことは鉄則です。分析中に「○○さんのミス」「担当者が新人だったから」など個人起因で片付けてしまうと、再発防止策が「個人への注意喚起」程度になり、本質的な解決になりません。それどころか「次も誰かが同じミスをしたらどうするのか」という問題が残ります。個人を責めれば雰囲気も悪くなり、以降の改善活動に支障が出る恐れもあります。そうではなく、なぜその人がミスをしたのか(教育や仕組みに問題はないか)という視点で、プロセスやシステム側の要因に目を向けることが重要です。原因は人ではなく仕組みに求め、「誰が悪いか」ではなく「どうすれば防げるか」を考えましょう。
- 多職種・現場の関係者で協力して行う: 分析作業には品質管理担当者だけでなく、実際の工程を知る作業者や関連部門のメンバーも巻き込んで行うと効果的です。現場の状況に詳しい人々の知見を取り入れることで原因の見落としが減り、実行可能な対策も立てやすくなります。異なる立場の人が参加することで、「現場ではこうなっている」「お客様の視点ではこうだ」といった多角的な視点から原因を検討でき、対策の納得感も高まります。チーム全員で問題を共有し解決に当たること自体が、職場の改善文化を育むことにもつながります。
- 実行可能な対策に落とし込む: 分析のゴールは原因を究明すること自体ではなく、再発防止策を講じて実行することです。導き出した対策が現場で無理なく実践できるか、必要なリソースや時間は確保できるかを考慮しましょう。実現不可能な理想論を掲げても意味がないので、現実的な範囲でベターな策を講じることが大切です。対策実施後はきちんと効果検証まで行い、必要なら追加措置を講じて問題を完全に潰し込む姿勢で臨みます。ここまで徹底して初めて、分析に費やした時間が現場の価値向上として報われるのです。
以上のポイントを意識するだけでも、なぜなぜ分析の質は格段に向上します。実践の場ではつい近道を取りたくなったりプレッシャーから早く結論づけたくなったりするものですが、上記のコツを思い出して丁寧に「なぜ?」を重ねてみてください。現場で誰もが実践者となり、協力して問題解決に当たることで、確実な再発防止と着実なカイゼンの効果が得られるはずです。
「意味がない」「パワハラだ」と言われる理由とその対策
なぜなぜ分析の有用性は広く認められていますが、一方で「なぜなぜ分析は意味がない」とか「結局はパワハラ(吊るし上げ)だ」といった否定的な声が聞かれることもあります。これらは主に、なぜなぜ分析が正しく実施されていない場合に起こる弊害です。ここでは、よくある失敗例とその対策について触れておきます。
- 表面的な原因で止まってしまう: 「なぜ?」を問いはしたものの、浅い原因で分析を終えてしまうケースです。例えば先述の機械トラブルの例でヒューズが切れた段階で止めてしまうような場合です。このように十分に深掘りせずに対策を考えてしまうと、根本的な解決には至りません。対策としては、「本当にそれが真因か?さらに背後に原因はないか?」と自問し、納得できるまで掘り下げる姿勢を持つことです。
- 思い込みや仮定に基づいた分析: 最初から「原因はきっと○○だろう」と決めつけてしまい、形だけ「なぜ?」を繰り返すケースです。この場合、問いと答えが論理でつながっておらず、都合の良い原因に誘導してしまう傾向があります。事実に基づかない分析は意味がなく、データや現場確認によって裏付けを取りながら進めることが必要です。
- 「なぜ?」を繰り返すだけで行動しない: 原因を突き止めたところで満足してしまい、改善策の実行に移さないケースです。原因究明そのものが目的化してしまうと、せっかく真因が分かっても再発防止につながりません。必ず対策の実行と効果検証までセットで完了と考え、行動まで起こすようにしましょう。
- 問題の範囲が広すぎる/曖昧: 問題設定が漠然としていて、問いが散漫になるケースです。例えば「売上を上げるためには?」といった大きすぎる問いだと、「なぜ売上が上がらないのか」を突き詰めるのは困難です。分析対象はできるだけ具体的な事象に絞り、範囲を限定しましょう(ポイントで述べた問題の明確化)。そうすることで原因の検討もしやすくなります。
- 個人攻め・詰問に陥ってしまう: 上司が部下を詰問する形で「なぜ○○しなかったんだ?」を繰り返すなど、責任追及の色彩が強くなってしまうケースです。これでは建設的な議論ではなくパワハラまがいになり、現場の士気を下げてしまいます。指摘されることを恐れてミスや問題を隠すようにもなり、かえって真因の究明が困難になります。対策は前述のとおり、決して特定の誰かを標的にしないことです。「なぜ○○さんはミスをした?」ではなく「なぜミスが発生したのか、その背景は?」と問い、個人ではなくプロセスの問題として捉えます。責任追及ではなく原因追及だという認識をチーム全員で共有しましょう。
以上のような失敗パターンは、裏を返せば前述したコツを守れば防げるものばかりです。実際、「なぜなぜ分析は意味がない」と言われるのは、これらのポイントを押さえずに実施して徒労に終わってしまったケースが目立つからに他なりません。正しく行えば決して無意味なものではなく、むしろシンプルながら強力な問題解決手法です。現場で実践する際は「形式的になぜを5回聞けばいい」というものではないことを念頭に置き、真因究明と再発防止策の実行まで一貫してやり遂げるようにしましょう。
まとめ:カイゼンにつなげるために明日からできること
なぜなぜ分析は、製造業の現場のみならずあらゆる職場で活用できる普遍的な問題解決力を養う手法です。トヨタの有名なエピソードが示すように、原因を根本から断つことで同じ過ちを繰り返さずに済み、結果的に現場の生産性と品質が向上します。表面的な対応で終わらせず「なぜ?」と問い続ける姿勢は、日々の業務改善(カイゼン)の原動力にもなります。現場で起きる大小様々な問題に対し、「これは現場を良くするチャンスだ」と捉えてみてください。問題の裏に潜む原因を探り、対策を講じるプロセスを通じて職場に学習と改善の文化が根付き、組織全体が強くなっていくでしょう。
明日からでもできる第一歩は、身近な問題に対してチームで「なぜ?」を繰り返してみることです。例えば製造ラインで不良品が出たなら、関係者を集めて一緒に原因を考え、「なぜ起きたのか」を掘り下げてみましょう。最初はうまく真因にたどり着けないかもしれません。しかし諦めず何度も実践することで、原因を論理的に追究する思考習慣が身についてきます。やがて「これなら効く対策が打てる!」という実感を得られるようになるはずです。現場の一人ひとりがこのプロセスを体得すれば、問題が起きても素早く本質を見抜き、再発を防ぐ打ち手を講じられるようになります。それはすなわち、カイゼンが日常業務に溶け込んだ強い現場を築くことにつながるのです。
最後に念頭に置いておきたいのは、「問題が起きたときこそ改善の好機」だという視点です。なぜなぜ分析は、その好機を逃さず次の成功につなげるための道具と言えます。現場で困りごとに直面した際には是非怖がらずに「なぜ?」と問いかけてみてください。今日よりも良い明日の現場を作るために、トヨタ式のこのシンプルな問いかけがきっと大きな力になるでしょう。そして、その積み重ねが現場発のカイゼンを生み出し、ひいてはビジネス全体の成長へとつながっていくのです。
なぜなぜ分析について学ぶ!学習コースのご紹介
カイゼンベースの学習コースでは、なぜなぜ分析に関する具体的な内容を動画や理解度テストにより学習することが可能です。詳細の学習や実践でのご活用をご検討の方は、是非ご活用ください。
学習コース「ps-01:アニメで学ぶなぜなぜ分析入門~Part1~」
なぜなぜ分析は、日々の業務や改善活動に欠かせない問題解決の技術です。本講座では、なぜなぜ分析の基本的な進め方や大前提となる考え方を学習できます。基礎を習得し、問題解決を正しく進める力を身につけましょう。
学習コースの詳細
Lesson1:なぜなぜ分析とは(7:36)
Lesson2a:なぜなぜ分析の前提事項 前編(7:11)
Lesson2b:なぜなぜ分析の前提事項 後編(7:32)
Lesson3:あるべき姿からのアプローチ(8:00)
Lesson4:原理原則からのアプローチ(8:14)
「Lesson1:なぜなぜ分析とは」の動画はどなたでもご視聴頂けます。
「Lesson2:なぜなぜ分析の前提事項 前編」の動画は無料会員登録を行うことでご視聴が可能になります。
学習コース「ps-02:アニメで学ぶなぜなぜ分析入門~Part2~」
本講座では、なぜなぜ分析における重要な7つのポイント、そしてヒューマンエラーについてお伝えします。再発防止に繋がる対策を導くために、なぜなぜ分析の知識を深め、問題解決力を向上させましょう。
学習コースの詳細
Lesson1:なぜなぜ分析の7つのポイント 前編(8:20)
Lesson2:なぜなぜ分析の7つのポイント 後編(8:52)
Lesson3:ヒューマンエラーとなぜなぜ分析-前提編-(6:50)
Lesson4:ヒューマンエラーとなぜなぜ分析-要因編-(8:53)
Lesson5:ヒューマンエラーとなぜなぜ分析-対策編-(8:39)
Lesson6:エラーを減らす工夫(10:34)
Lesson7:なぜなぜ分析練習問題
「Lesson1:なぜなぜ分析の7つのポイント 前編」の動画はどなたでもご視聴頂けます。
「Lesson2:なぜなぜ分析の7つのポイント 後編」の動画は無料会員登録を行うことでご視聴が可能になります。
資料請求はこちらから
サービス紹介資料・価格表を無料でダウンロードできます。お気軽にお問い合わせください。
.png)
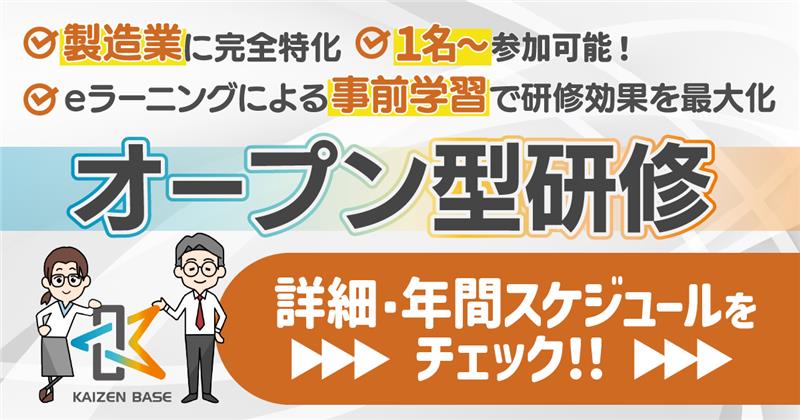
関連学習動画
-
ps-02
アニメで学ぶなぜなぜ分析入門~Part2~
公開講座
Lesson1:なぜなぜ分析の7つのポイント 前編
受講対象者
全部門(一般/中堅/管理職)- カリキュラム構成
-
- はじめに
- なぜなぜ分析の7つのポイント
- ①文章を簡潔に書く
- ②事象を混在させない
- ③逆から読んで意味が通っているか確認する
- まとめ
-
ps-02
アニメで学ぶなぜなぜ分析入門~Part2~
無料会員限定
Lesson2:なぜなぜ分析の7つの ポイント 後編
受講対象者
全部門(一般/中堅/管理職)- カリキュラム構成
-
- はじめに
- ④再発防止に繋がるまでなぜを繰り返す
- ⑤本質からずれた分析をしない
- ⑥心理面への原因追及はしない
- ⑦悪いという言葉は使わない
- まとめ
-
ps-02
アニメで学ぶなぜなぜ分析入門~Part2~
公開講座
Lesson3以降は、有料会員サービスで限定公開中!
受講対象者
全部門(管理職向け)- カリキュラム構成
-
アニメで学ぶなぜなぜ分析入門~Part2~
Lesson1:なぜなぜ分析の7つのポイント(前編)
Lesson2:なぜなぜ分析の7つのポイント(後編)
Lesson3:ヒューマンエラーとなぜなぜ分析-前提編-※有料会員限定
Lesson4:ヒューマンエラーとなぜなぜ分析-要因編-※有料会員限定
Lesson5:ヒューマンエラーとなぜなぜ分析-対策編-※有料会員限定
Lesson6:エラーを減らす工夫※法人向け限定
-
ps-01
アニメで学ぶなぜなぜ分析入門~Part1~
公開講座
Lesson1:なぜなぜ分析とは
受講対象者
全部門(一般/中堅/管理職)- カリキュラム構成
-
- はじめに
- なぜなぜ分析とは
- なぜなぜ分析の基本
- なぜなぜ分析の狙い
- まとめ
-
ps-04
アニメで学ぶトヨタ生産方式 中級編 問題解決8ステップ Part2
無料会員限定
Lesson2:Step5 対策案検討とスケジュール策定
受講対象者
全部門(係長/次長・課長)- カリキュラム構成
-
- はじめに
- Step5におけるポイント
- 対策案検討の視点
- スケジュール策定のコツ
- まとめ
-
ps-04
アニメで学ぶトヨタ生産方式 中級編 問題解決8ステップ Part2
公開講座
Lesson3以降は、有料会員サービスで限定公開中!
受講対象者
全部門(係長/次長・課長)- カリキュラム構成
-
アニメで学ぶトヨタ生産方式 中級編 問題解決8ステップ Part2
Lesson1:Step4 真因の特定(なぜなぜ分析)
Lesson2:Step5 対策案検討とスケジュール策定
Lesson3:Step6 対策の実行※法人向け限定
Lesson4:Step7 効果の確認と評価※法人向け限定
Lesson5:Step8 標準化と横展開※法人向け限定